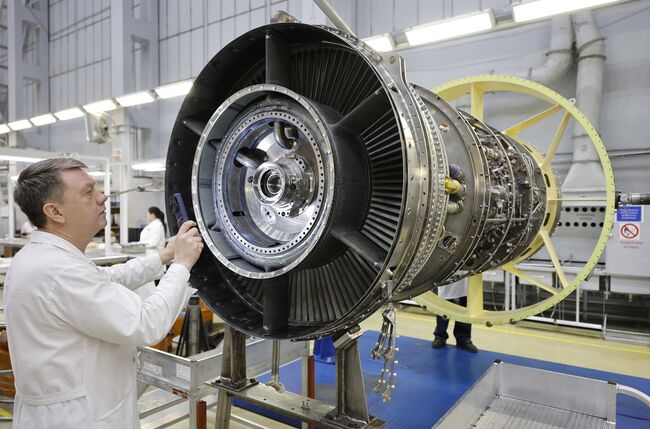
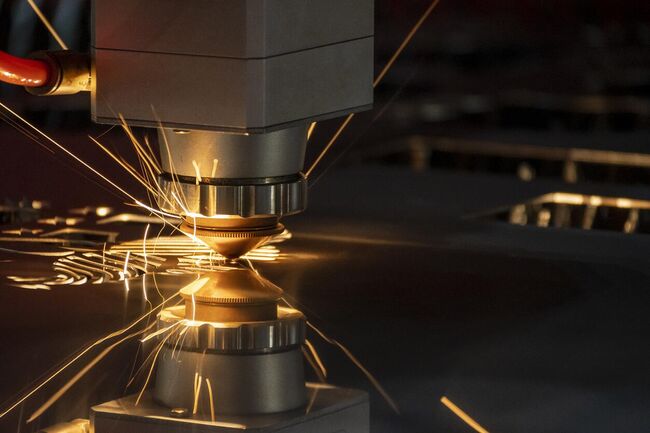
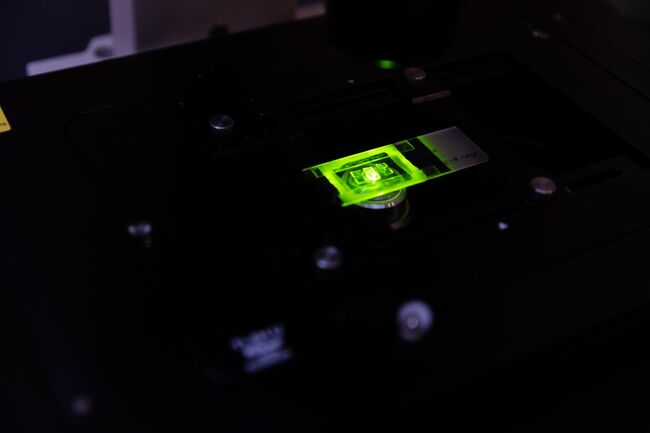
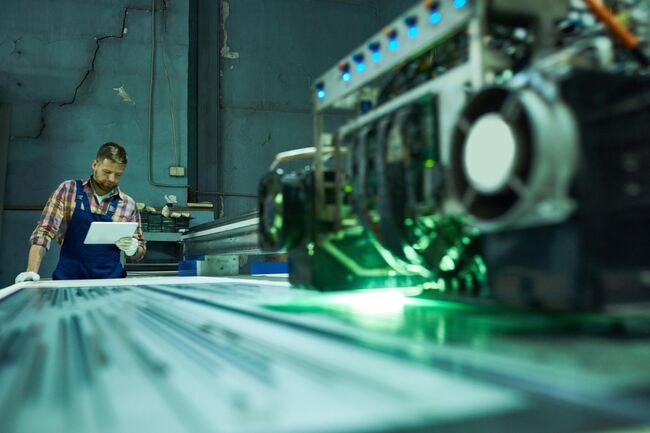
Придумано в России: от изобретения до производства
Прорывные технологии, обеспечивающие лидерство страны, возможны только на основе прикладной науки. Как перекинуть тот самый мостик между академическим университетом и промышленностью, чтобы научная идея вышла в мир и принесла пользу, а не погибла в "долине смерти" научно-технических разработок? Корреспондент РИА Новости побывал в Санкт-Петербургском политехническом университете Петра Великого и собрал истории трех конкретных изобретений, которые прошли кратчайший путь от замысла до внедрения.

Топливные форсунки для газотурбинных установок
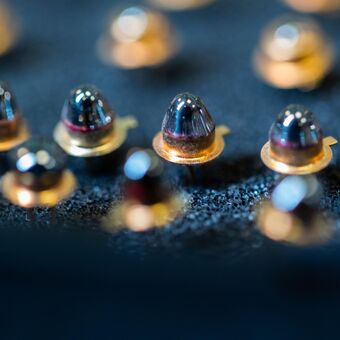
Микролинза для газового сенсора
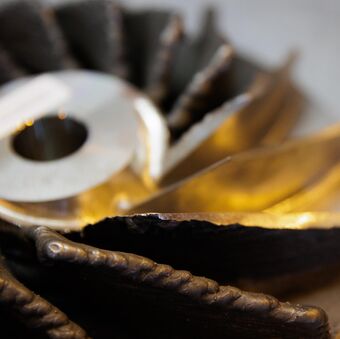
Российская крыльчатка для высоконагруженных компрессоров
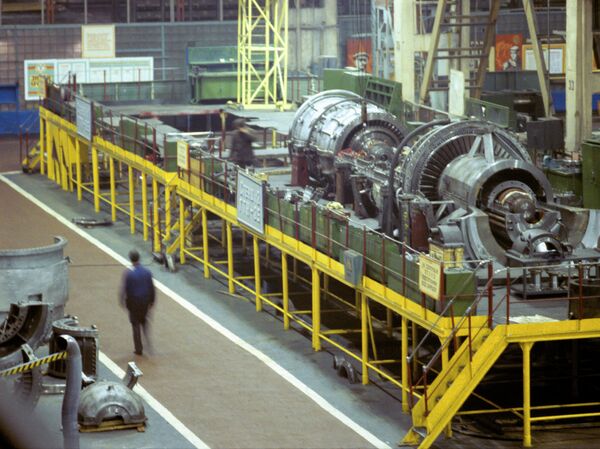
В газоперекачивающем агрегате есть компрессор, который нагнетает давление газа и дальше его транспортирует. Чтобы привести этот компрессор в движение, нужен газотурбинный двигатель, работающий на энергии, которая получается при сжигании природного газа. Сам газ сжигается в камерах сгорания, а топливо туда поступает с помощью топливных форсунок с торцевой крышкой.
Эти форсунки и были разработаны учеными СПбПУ
"Сейчас ведется много дискуссий по поводу "долины смерти" научно-технических разработок (так называют участок пути от лабораторного прототипа к серийному образцу. – Прим. ред.). Некоторые коллективы, действительно, занимаются наукой ради науки. У нас же получилось создать мощный конгломерат, в который финансово вошли крупный технический заказчик, государство в лице "Приоритет-2030" и сам университет"
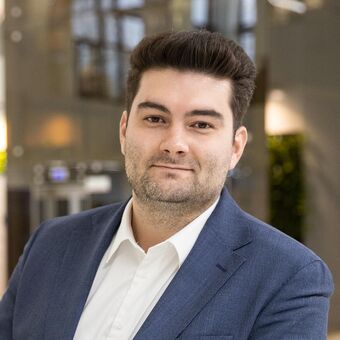
Павел Новиков
Директор НОЦ "Машиностроительные технологии и материалы" СПбПУ
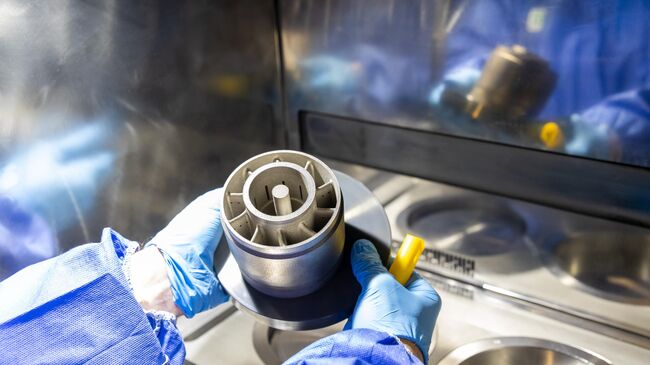
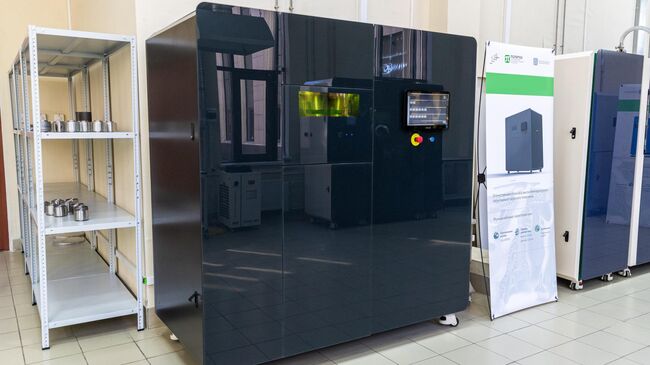
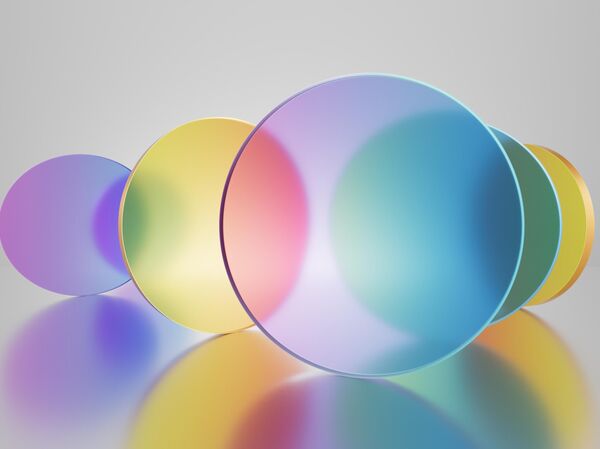
Мировой рынок инфракрасных материалов составляет примерно 400 миллионов долларов в год с прогнозом роста в 8,6%, причем 75% рынка занимают именно стеклообразные материалы. Стимулом для развития инфракрасной оптики стало широкое внедрение систем ночного видения и тепловизионной аппаратуры.
"Наша задача – решить проблему стыковки инфракрасных излучателей и фотоприемников с оптическими элементами таким образом, чтобы на выходе получился хороший прибор. В первую очередь мы получили новый оптический элемент для газового сенсора – микролинзу, которая имеет множество ноу-хау. Во-первых, она состоит из нескольких слоев стекла, а это позволяет выдерживать необходимый диапазон температур сенсора. Во-вторых, сама форма стекла стандартизирована, и мы ее выдерживаем от сенсора к сенсору с высокой точностью. В-третьих, при изготовлении микролинзы исключается операция полировки, поскольку мы фактически наплавляем линзу на поверхность"
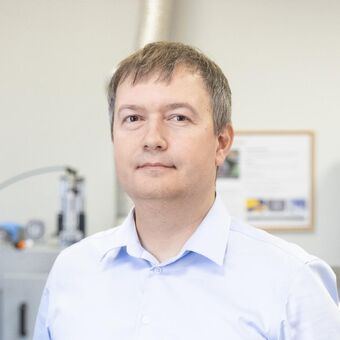
Александр Семенча
Директор НОЦ "Нанотехнологии и покрытия Института машиностроения, материалов и транспорта" СПбПУ
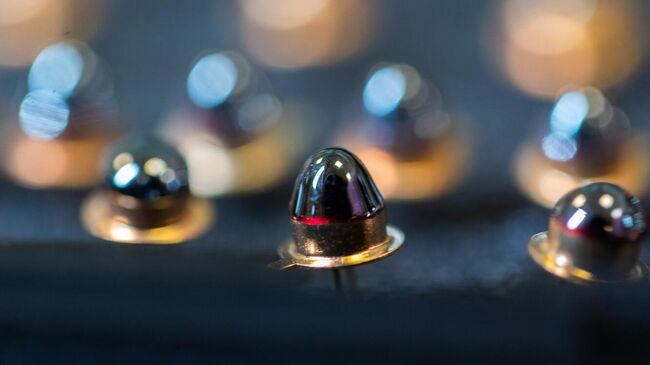

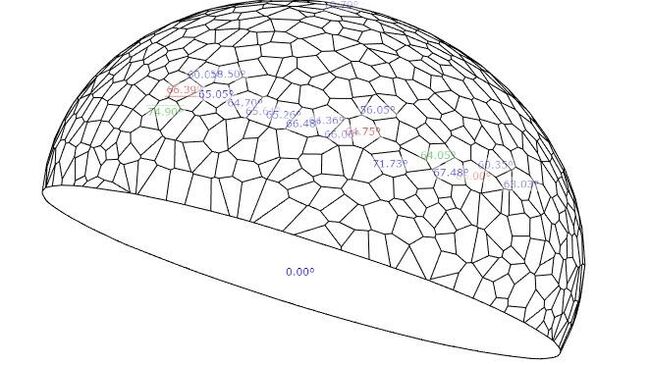
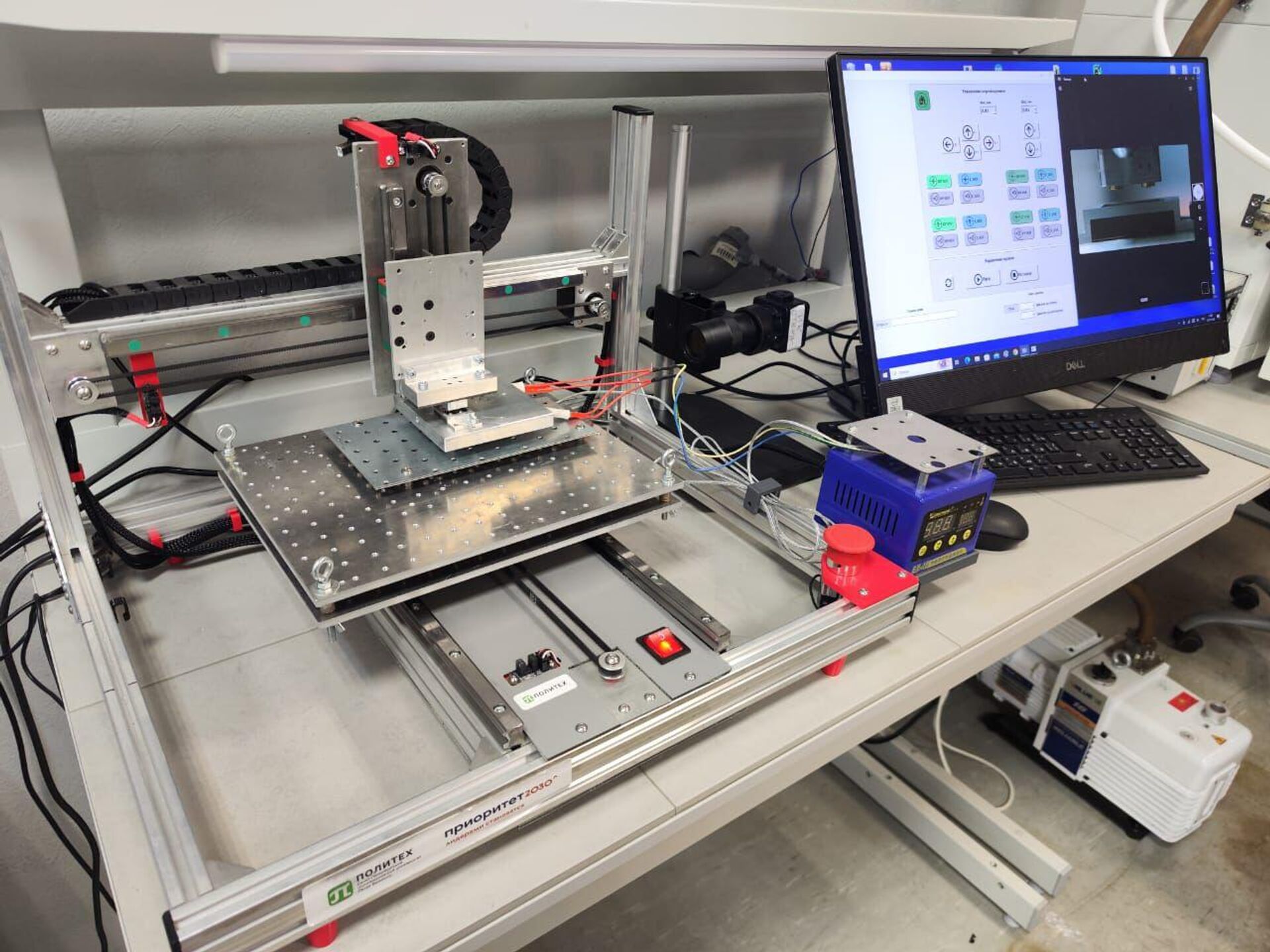
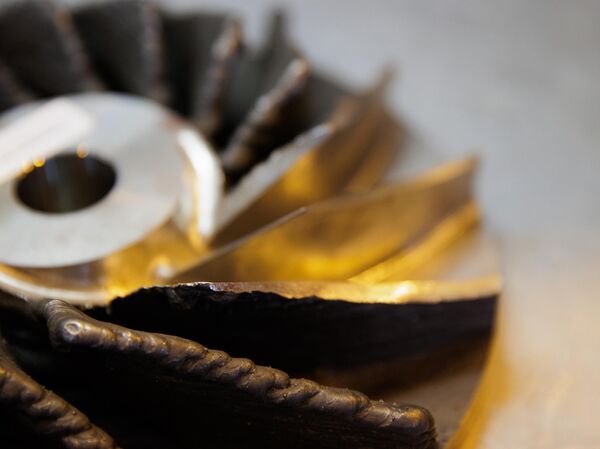
Крыльчатка – часть компрессорного устройства. В любом центробежном компрессоре есть различные участки, в которых при помощи крыльчатки перемещается воздух или газовая смесь. Помимо компрессорной техники они широко используются в подводной технике и водных плавсредствах, например в водомете водных мотоциклов. То есть крыльчатки – это целое семейство изделий, которые отличаются друг от друга количеством лопастей, высотой, направлением, формой, материалами и пр.
"Мы все существенно ускорили и удешевили. Нам требуется один день человеческой работы, для того чтобы изделие было напечатано в небольших габаритах. Если говорить про крупные размеры и сравнивать их с классическим подходом, то экономия производства такого изделия может составлять миллион рублей"
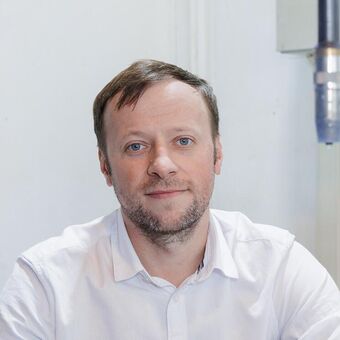
Олег Панченко
Заведующий лабораторией легких материалов и конструкций СПбПУ
Новая российская крыльчатка для высоконагруженных компрессоров
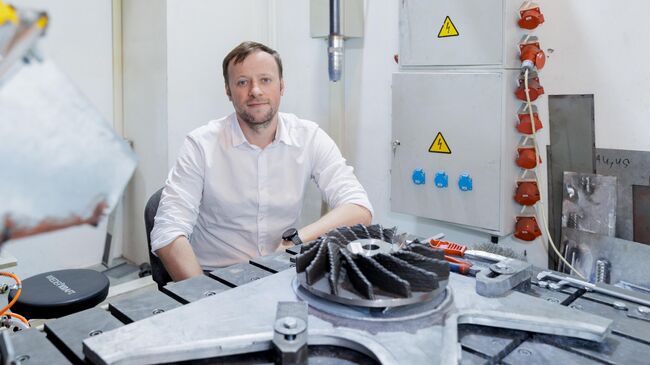
Универсальный станок для механической обработки изделий
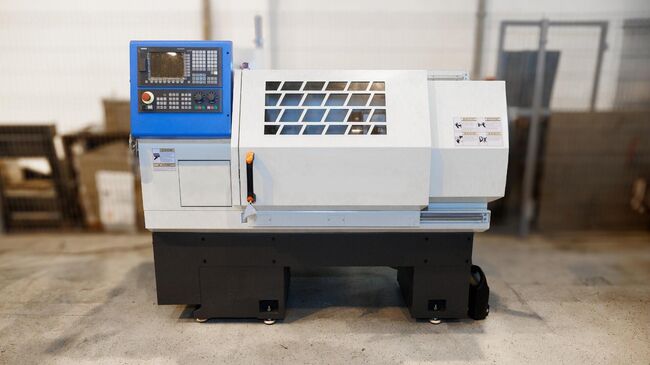
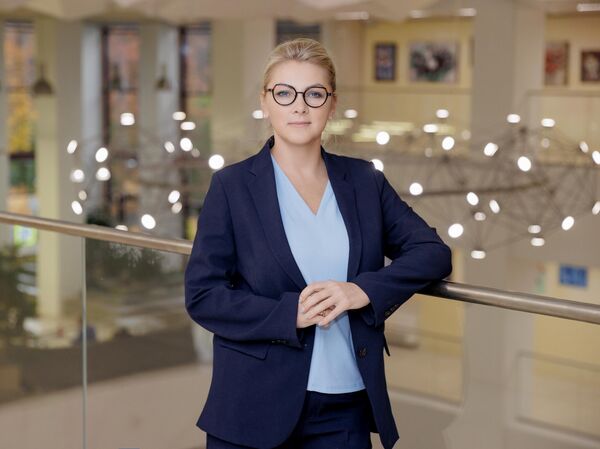
О коммуникации между университетом и промышленными партнерами
Мария Врублевская
и. о. проректора по перспективным проектам СПбПУ
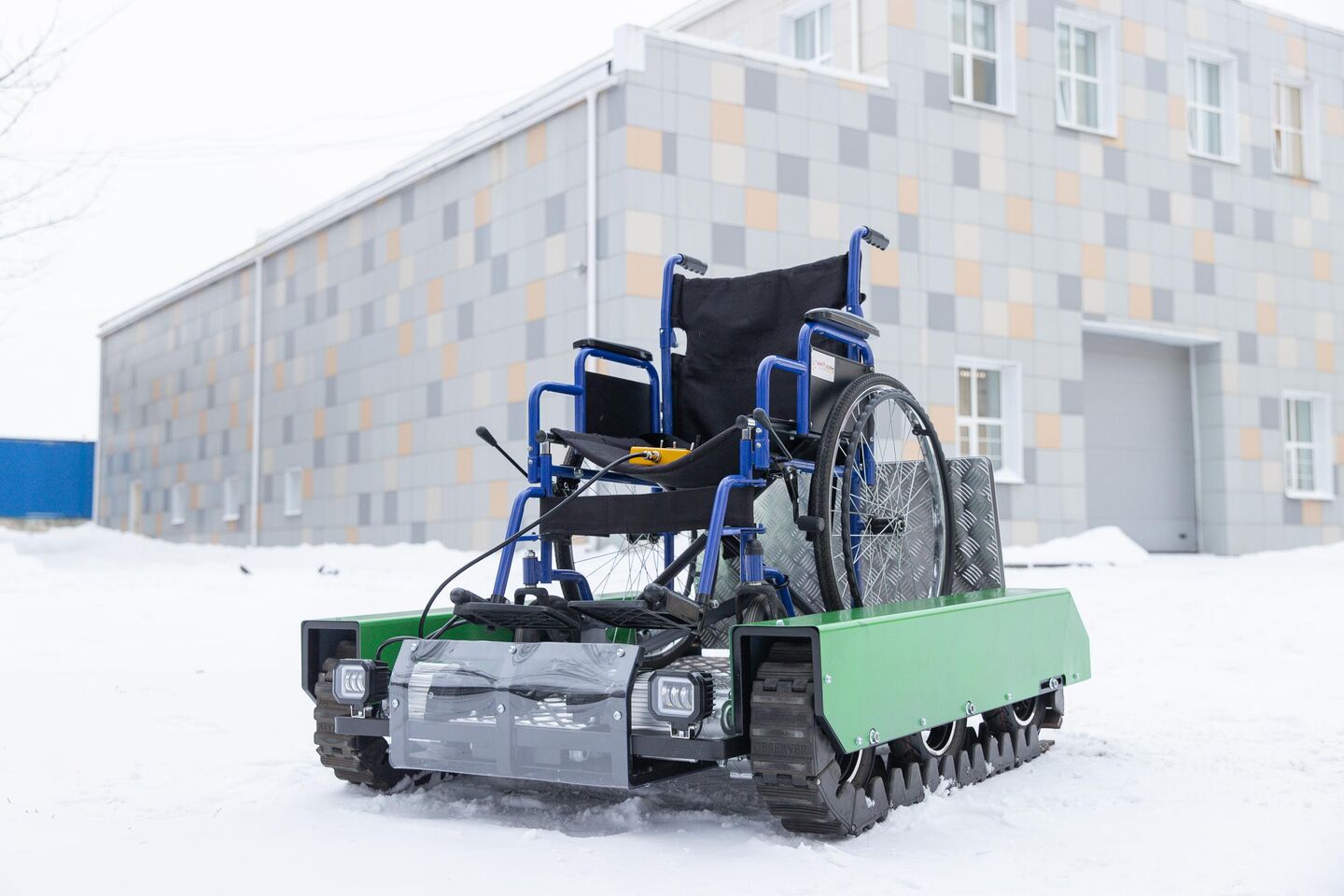
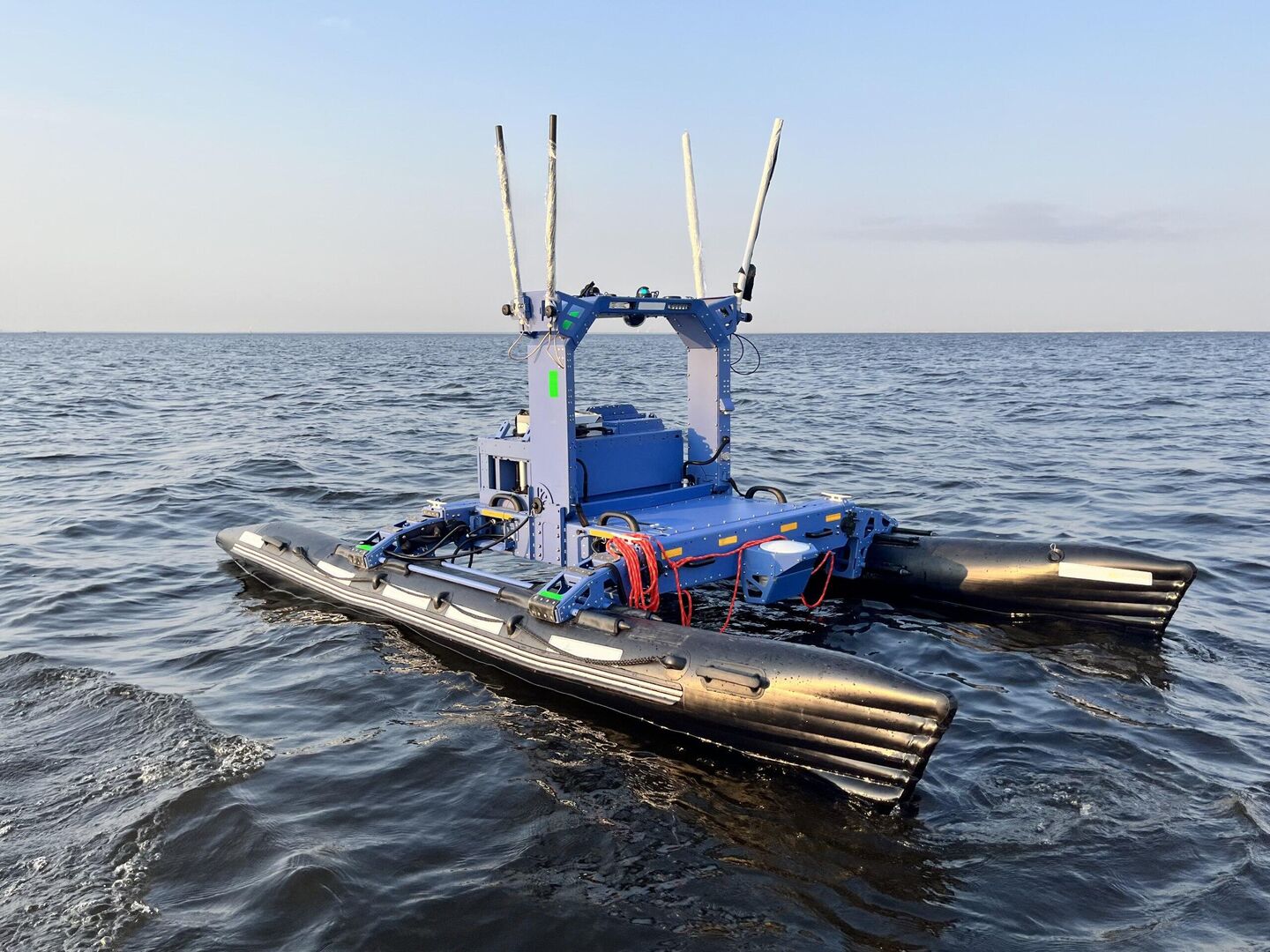