Ферма «Аллигаторов»
Репортаж с производства ударных вертолетов Ка-52
Андрей Станавов
Два несущих винта, два летчика и длинный список боевых задач, решить которые под силу только этой машине, — разведывательно-ударные вертолеты Ка-52 продолжают отвоевывать места на аэродромах армейской авиации ВКС России. Чтобы получше ознакомиться с процессом их производства, корреспондент РИА Новости отправился в Приморье и посетил завод Арсеньевской авиационной компании «Прогресс» холдинга «Вертолеты России» — «Аллигаторов» и их морскую версию «Катран» делают только здесь.
Короли вихрей
Если танк начинается с башни, то вертолет — с несущего винта. И хотя, на первый взгляд, ничего сложного в лопастях нет, стран в мире, обладающих технологиями их производства, — по пальцам пересчитать. Соосная схема — отдельная история. Только Россия выпускает такие машины серийно.
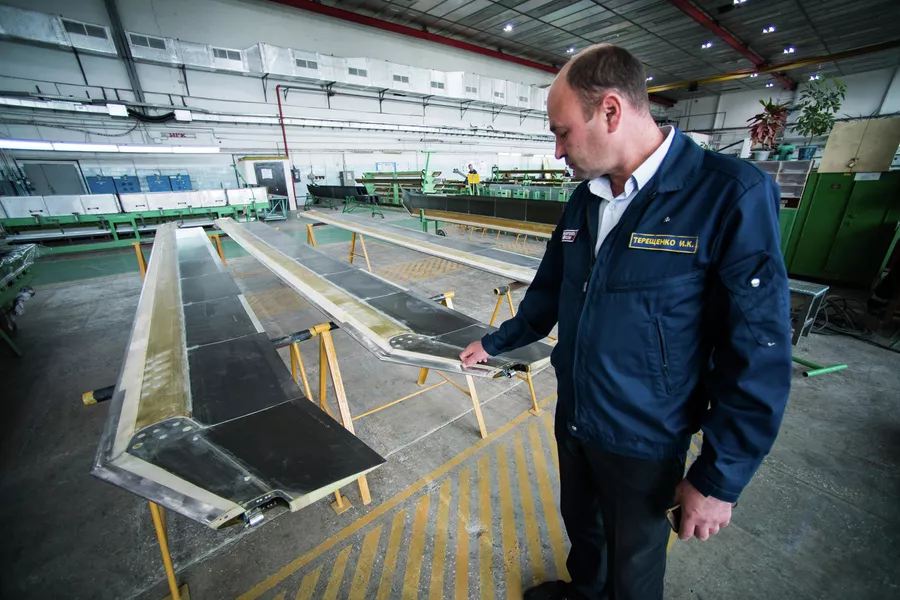
«Лопасти на вертолете Ка-52 полностью композитные, — объясняет РИА Новости начальник цеха по изготовлению деталей из полимерно-композиционных материалов Иван Терещенко. — Сначала изготавливаем силовую основу лопасти — лонжерон. Он сложный, включает в себя антиобледенительный нагревательный элемент, антифлаттерные грузы, оковки. Все это спаиваем в одно целое, после чего приклеиваем хвостовые секции и стреловидные законцовки».
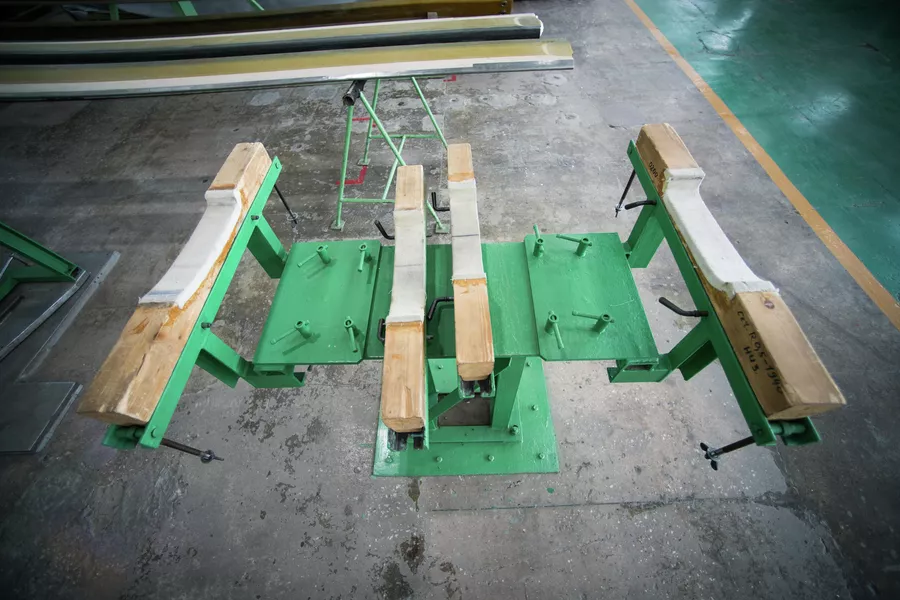
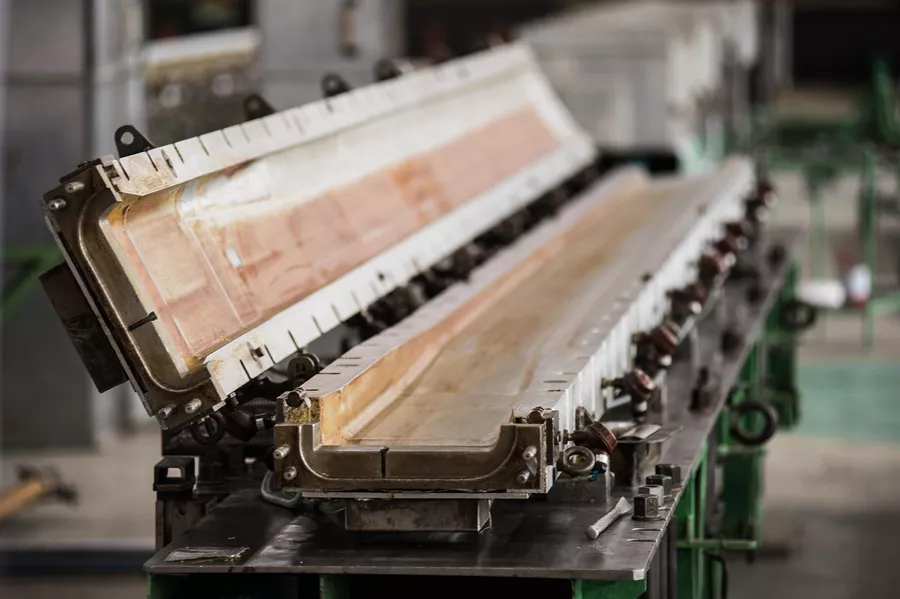
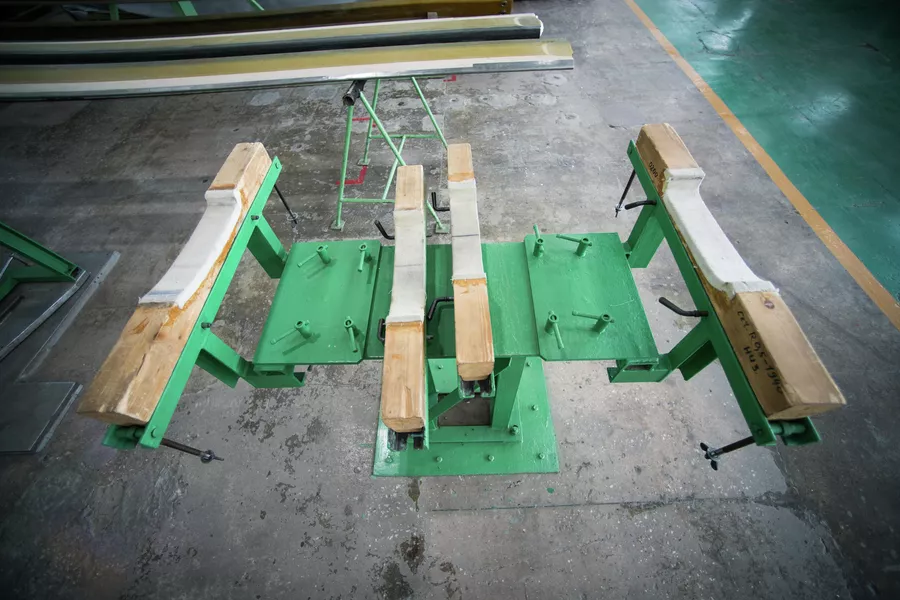
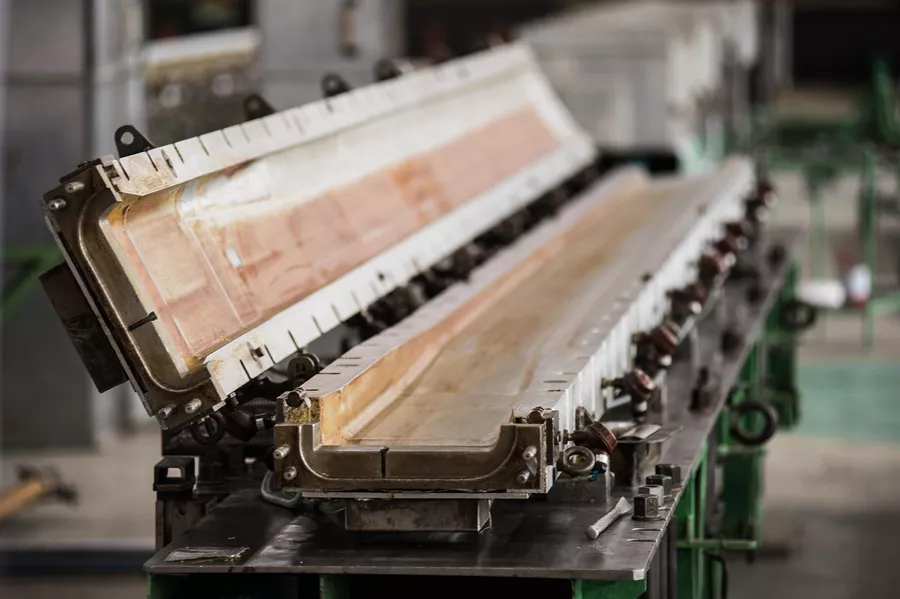
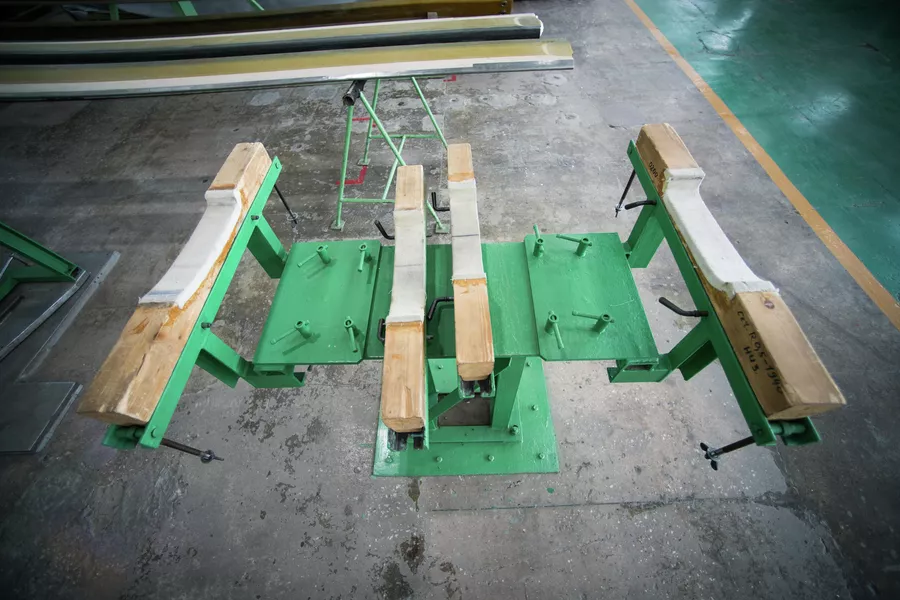
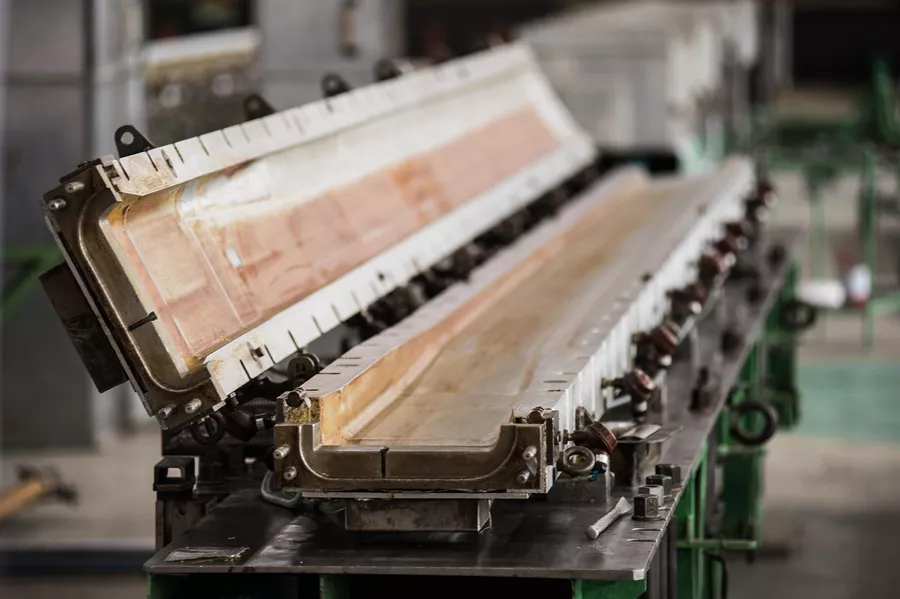
Готовую лопасть зачищают шкуркой, припаивают крышки, прокладывают провода для контурных огней и отправляют на покраску. Работа с композитами считается вредной, поэтому цех утопает в зелени комнатных растений. Десятки разнокалиберных горшков расставлены на полу вдоль рабочих мест, на подоконниках, стеллажах и станках.
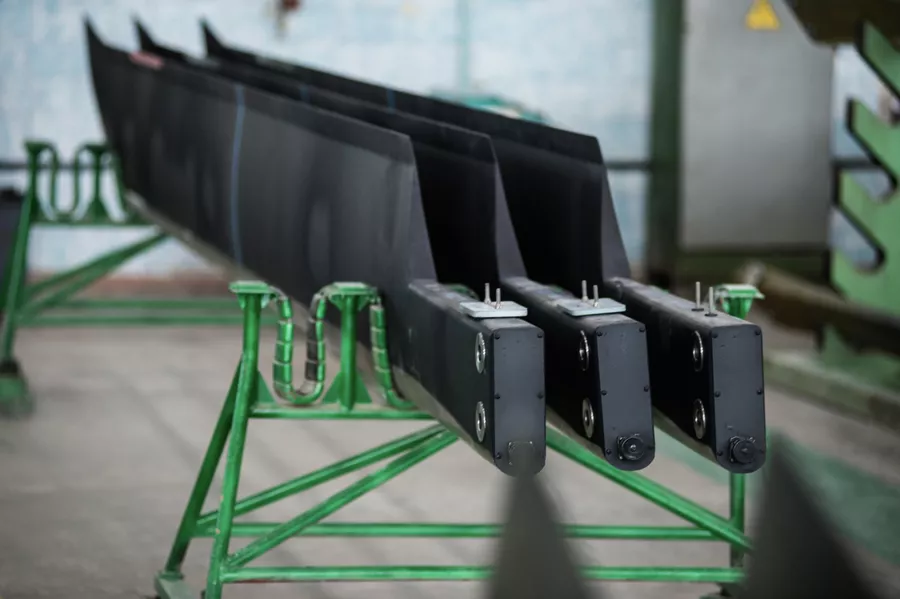
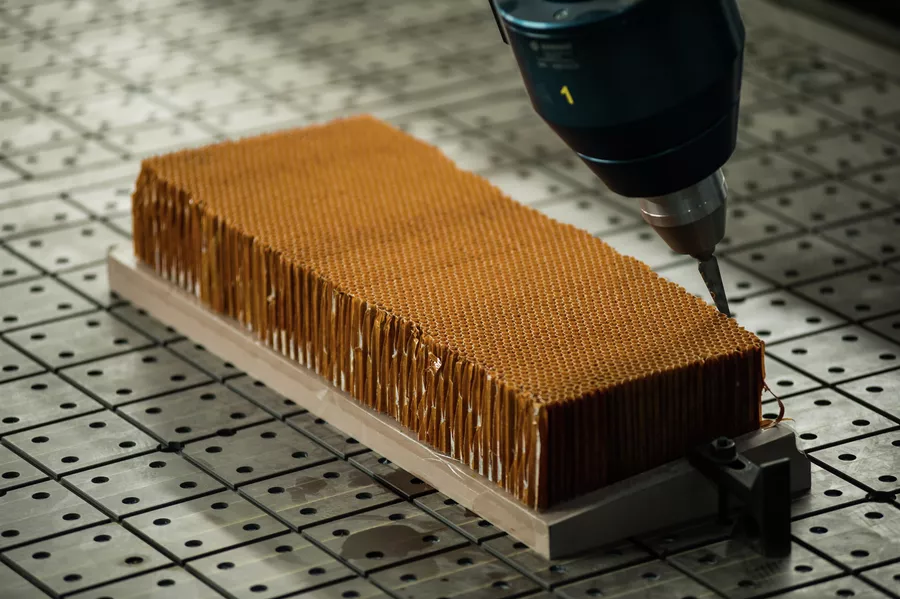
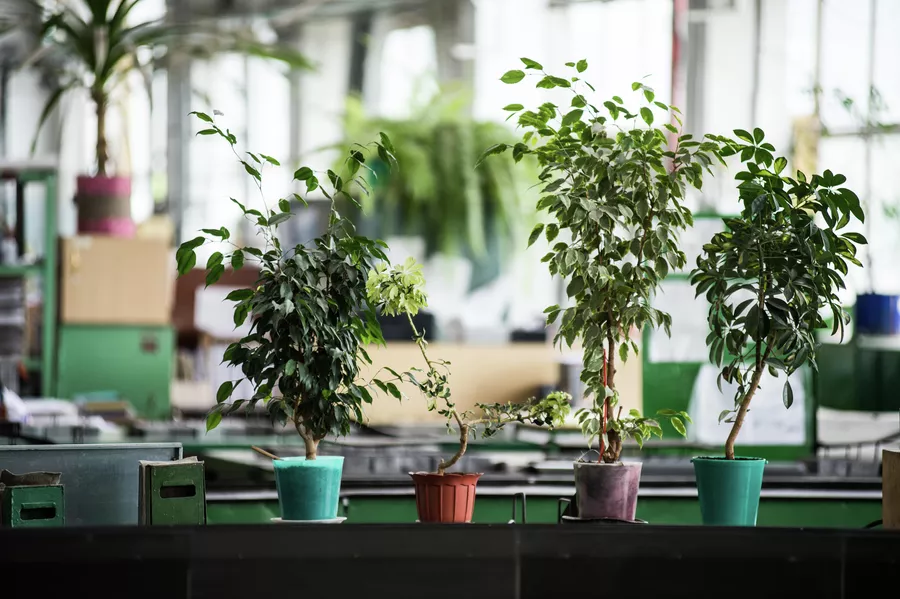
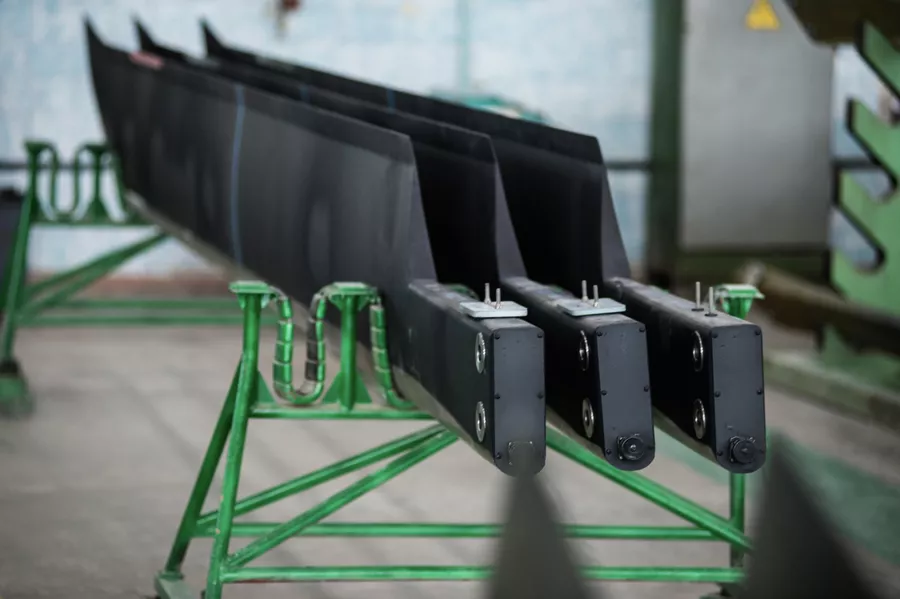
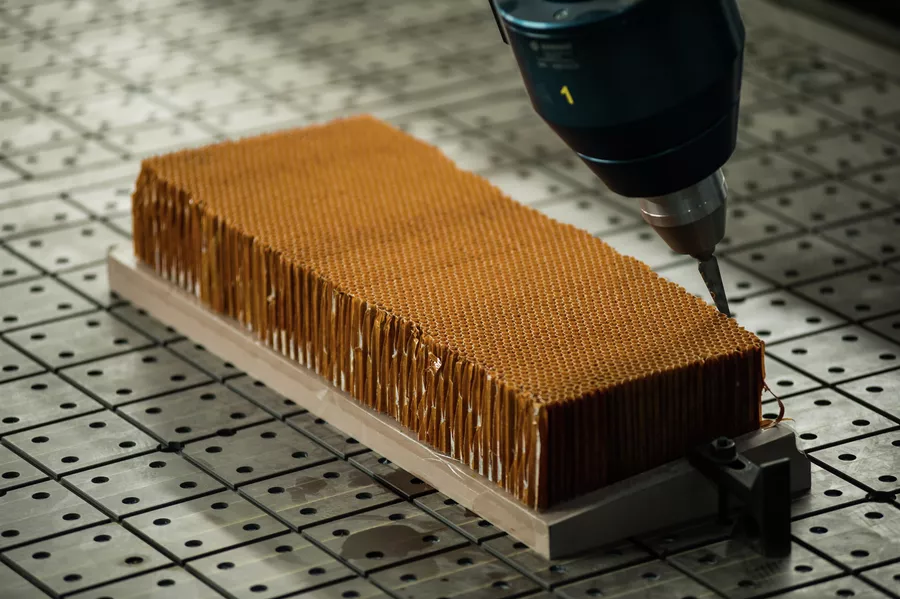
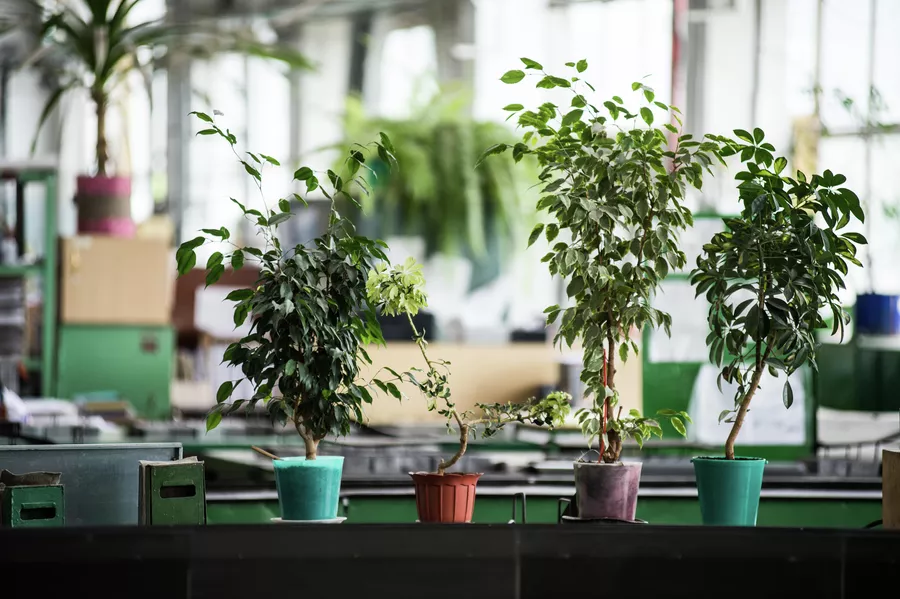
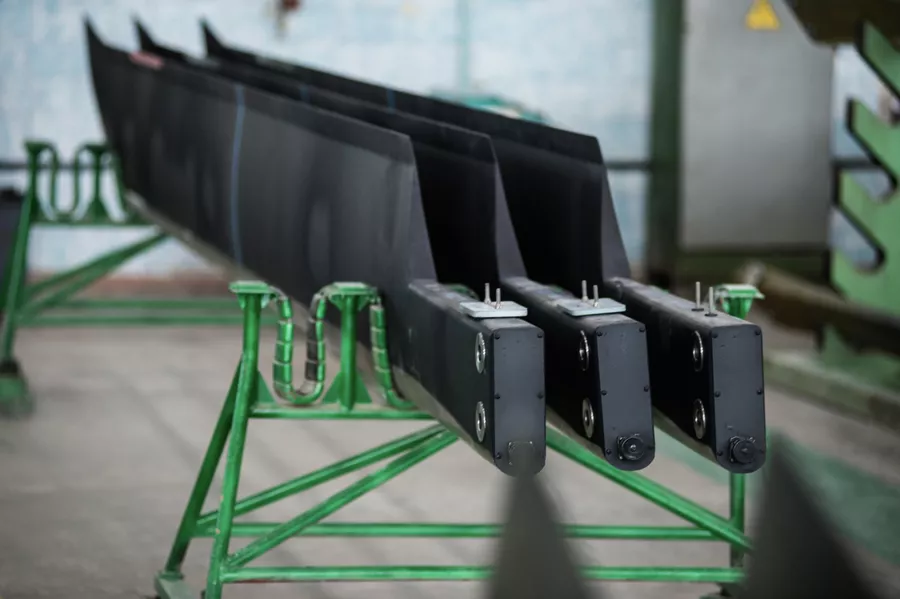
И хотя между собой сотрудники называют эту линию лопастным производством, делают тут не только лопасти — вертолет Ка-52 состоит из композитов более чем наполовину. Элементы обшивки, капоты, лючки, хвостовая балка — практически вся «шкура» «Аллигатора» сшита из плотных слоев стеклоткани и проложенных между ними легких сотовых панелей. Броня навешивается отдельно.
«Сырую стеклоткань выкладываем в оснастку нужной формы, добавляем сотовый наполнитель, склеиваем, упаковываем этот «пирог» в вакуумный пакет и отправляем в автоклав на запекание, — Иван открывает двери в зал с большими цилиндрическими печами. — Композиты удобны в обработке: не надо ничего гнуть, фрезеровать. Кроме того, они чрезвычайно прочные — даже при появлении трещины лопасть не разлетится на куски. Заметно выигрывают у металла по массе. К примеру, при длине семь метров лопасть Ка-52 весит всего 74 килограмма».
Заклепка к заклепке
Чтобы деталь приобрела необходимую прочность, ее 12 часов запекают при температуре 120-170 градусов Цельсия и под давлением до семи атмосфер. На заводе три автоклава, персонал работает круглосуточно, в три смены. Как только из печей извлекают готовые изделия, на их место сразу же загружают сырые.
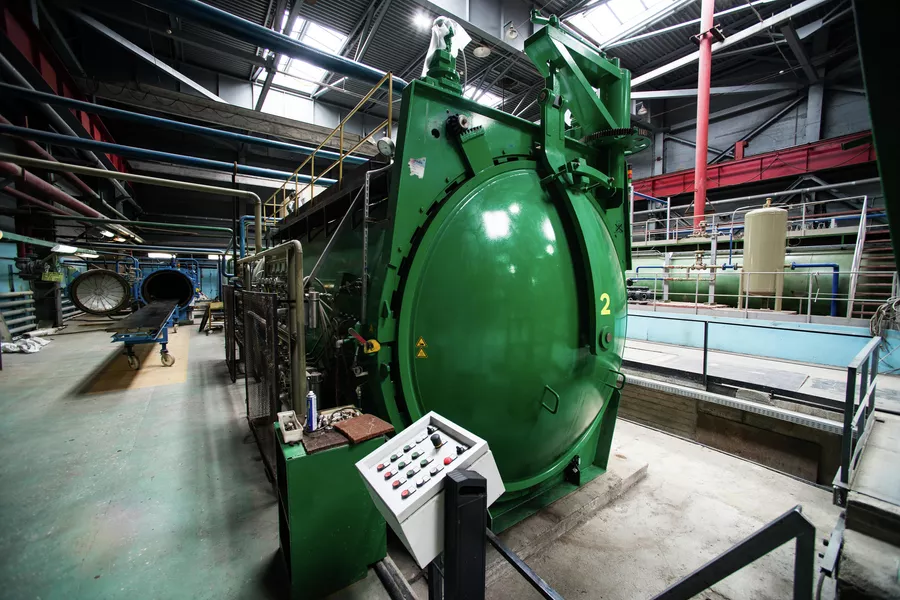
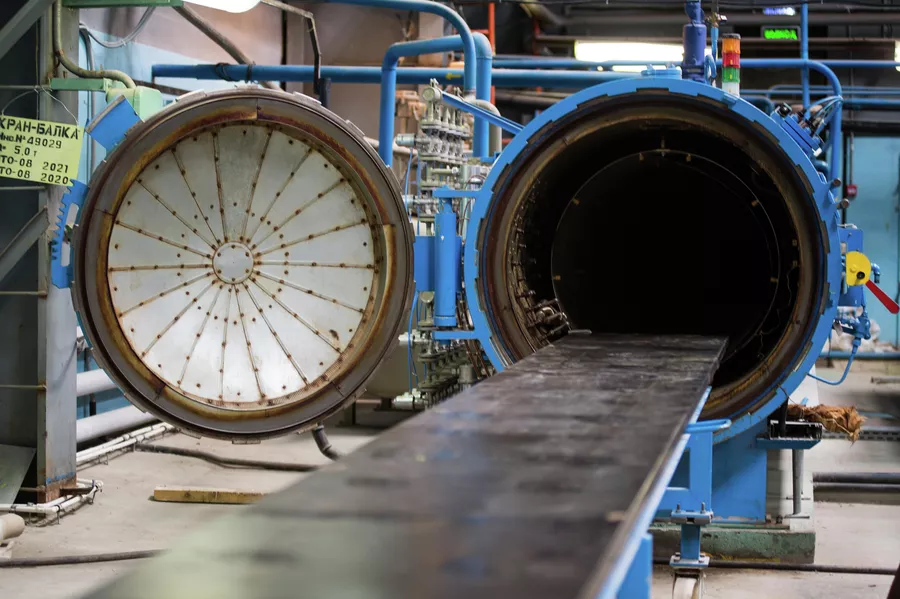
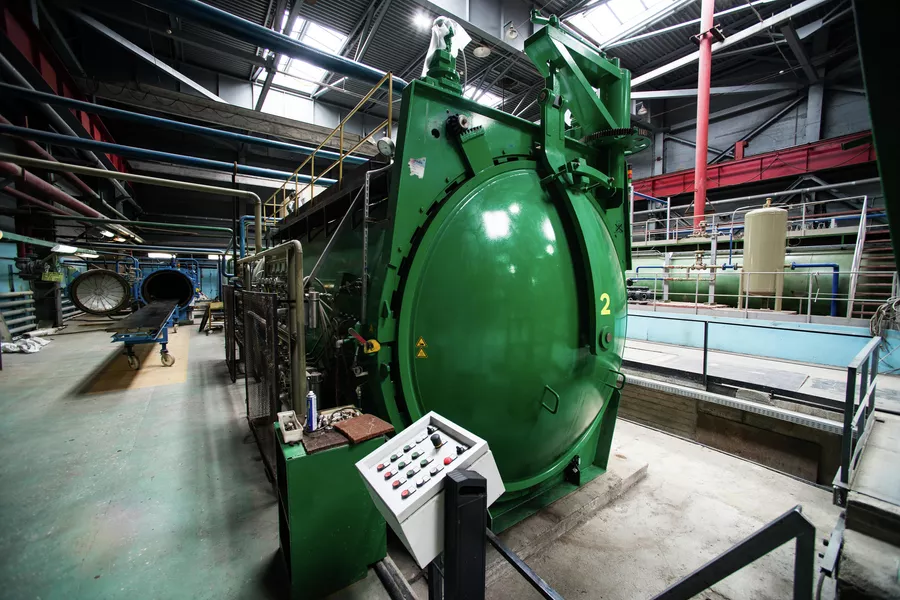
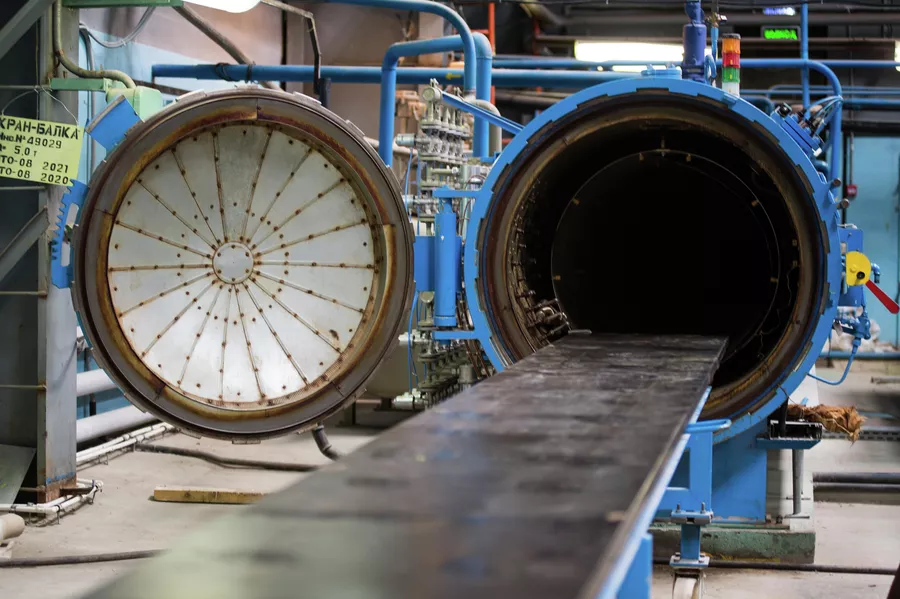
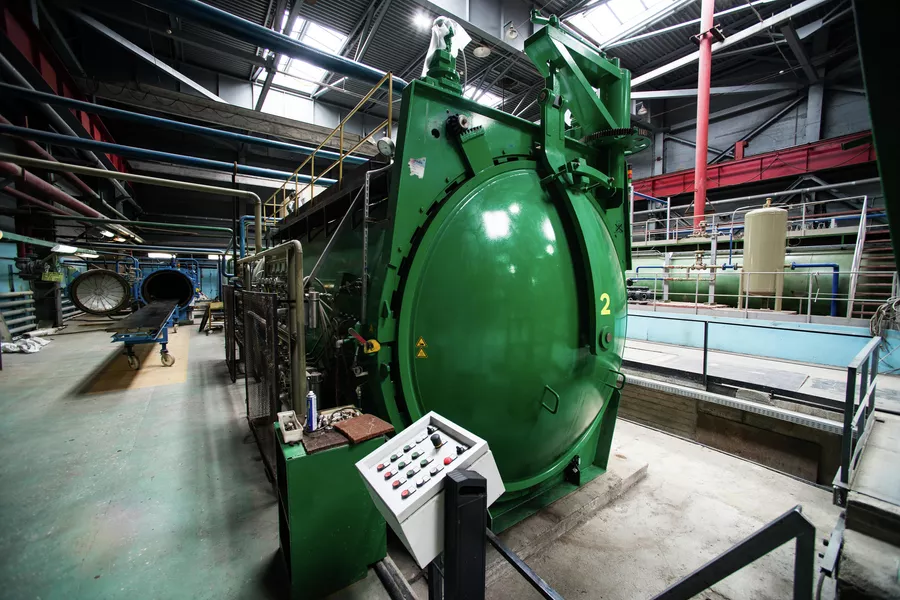
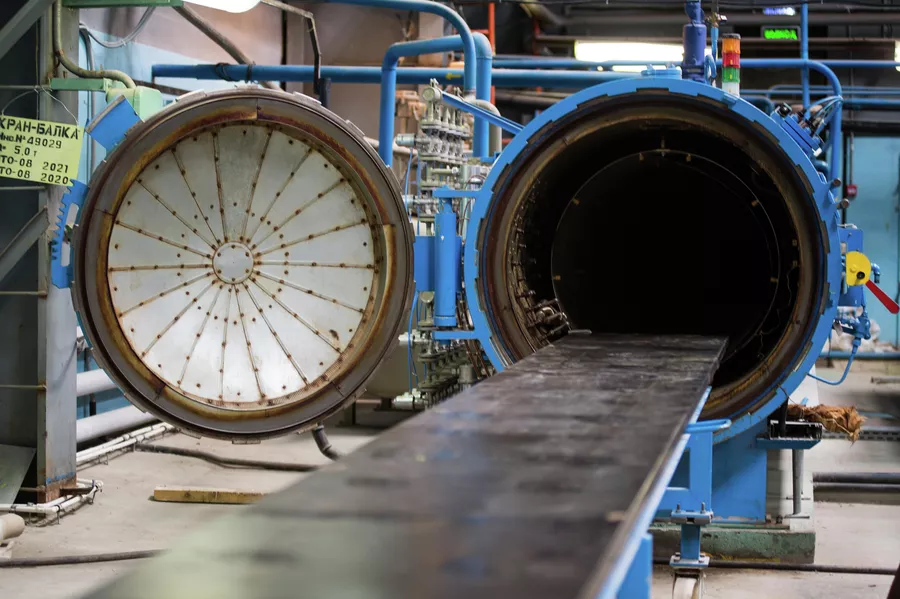
Из-за вязкости и волокнистости запеченные композиты пилить сложно — быстро забиваются зубья пилок. На «Прогрессе» пошли другим путем: доверили резку специальному роботу, который рассекает стекловолокно мощной струей воды, смешанной с мелким песком.
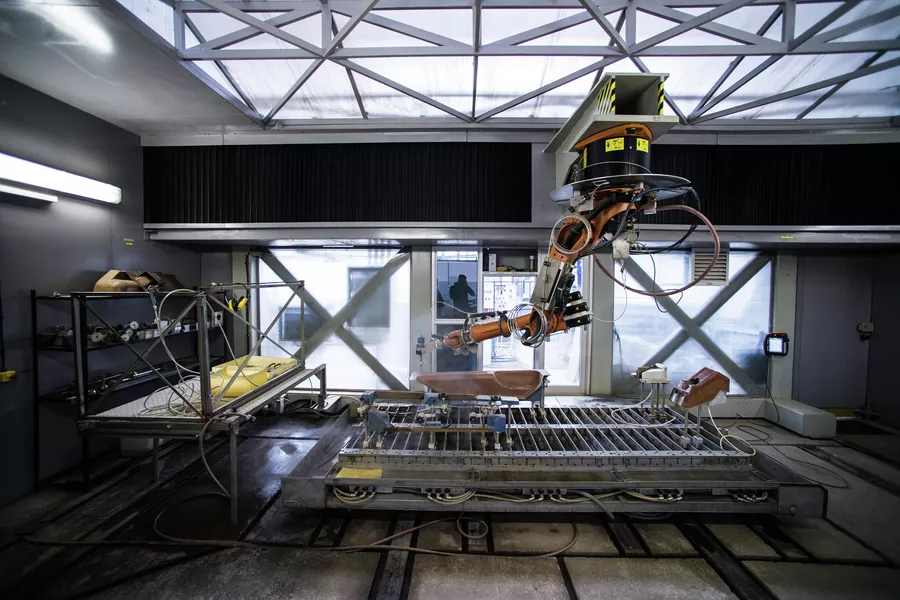
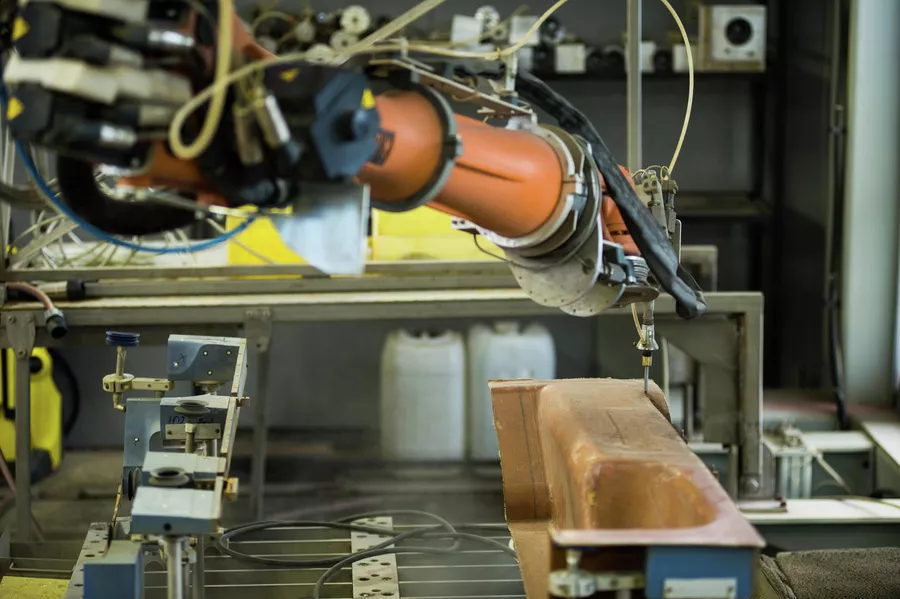
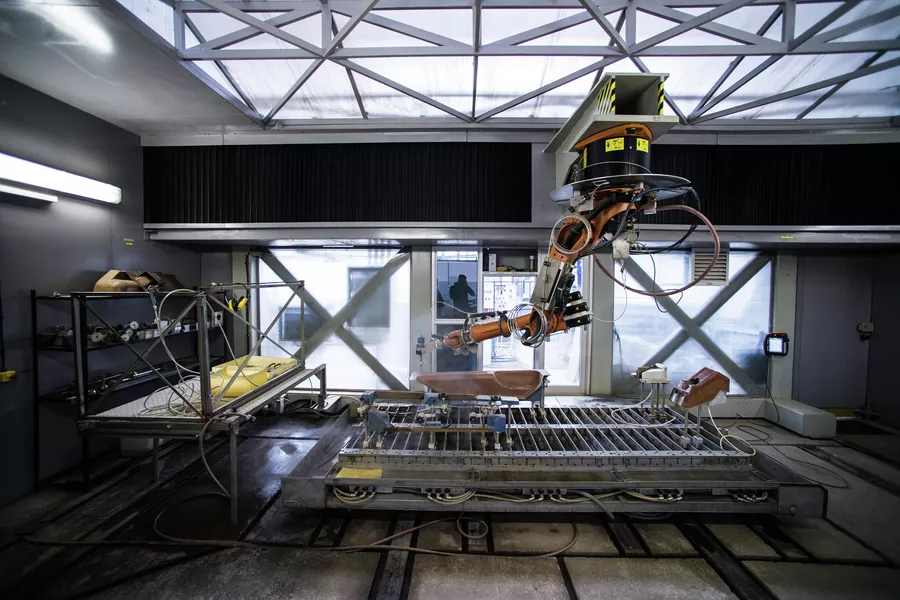
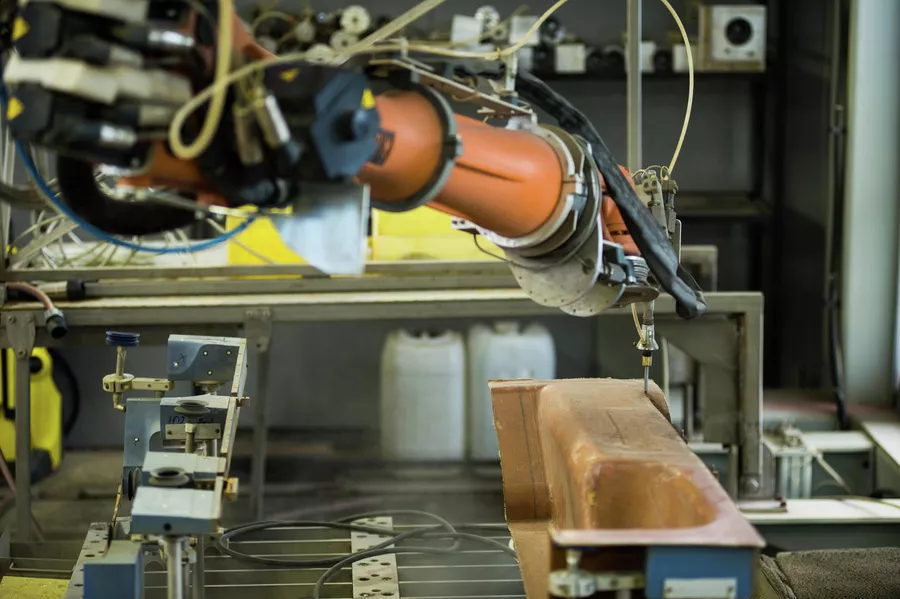
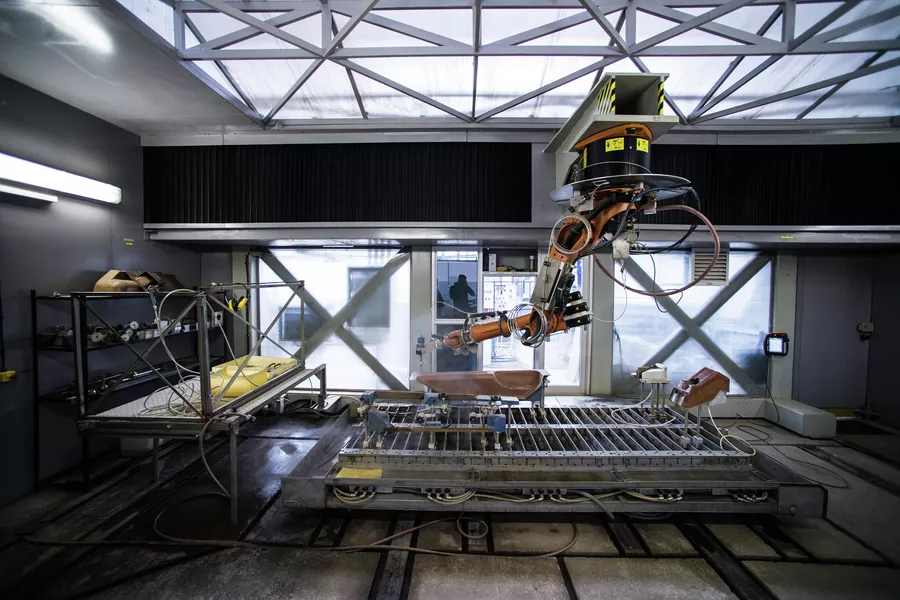
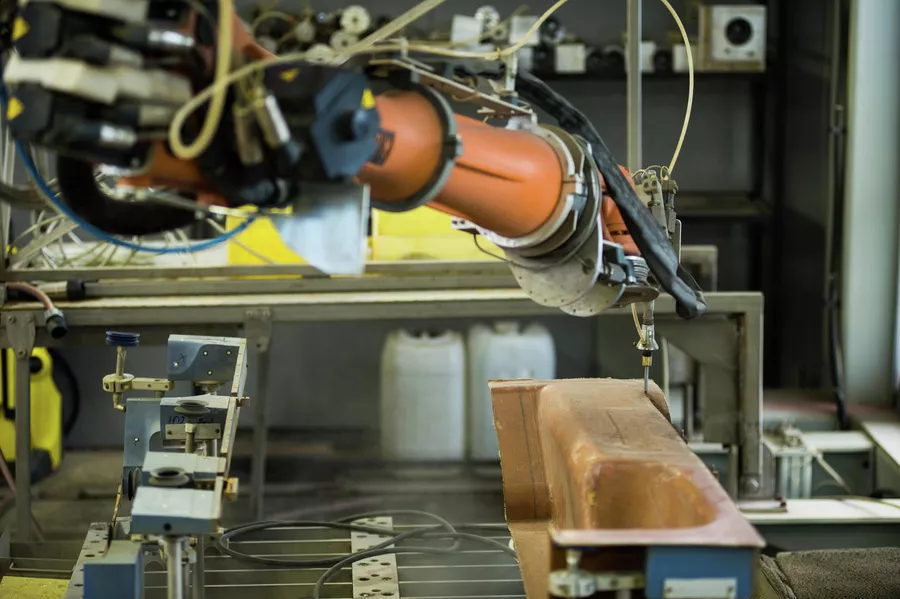
Рабочие уверяют, что робот этой струей может разрезать даже металл, но демонстрировать не стали.
Из цеха лопастного производства готовые композитные детали отправляются прямиком в агрегатно-сборочный цех, где их по чертежам приклепывают к стальным шпангоутам фюзеляжа.
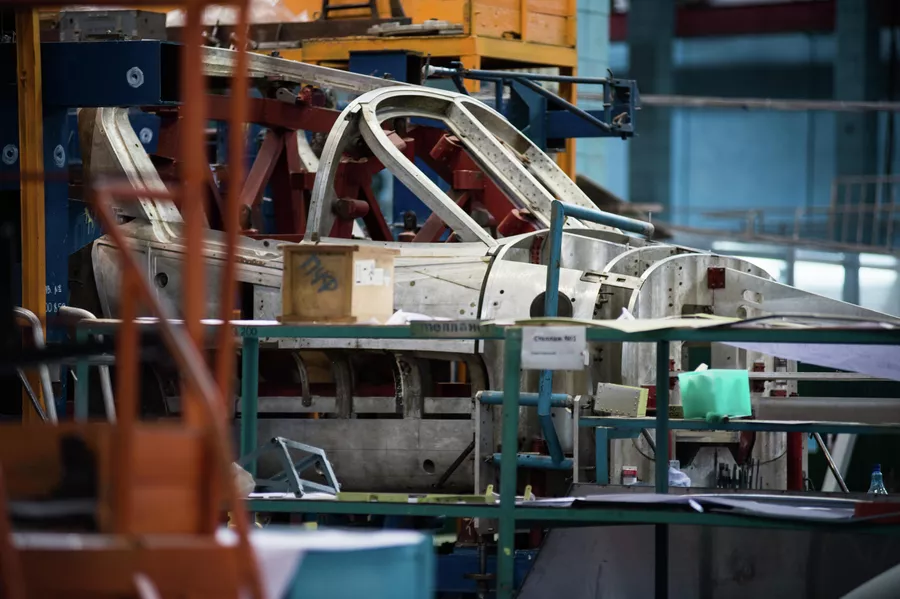
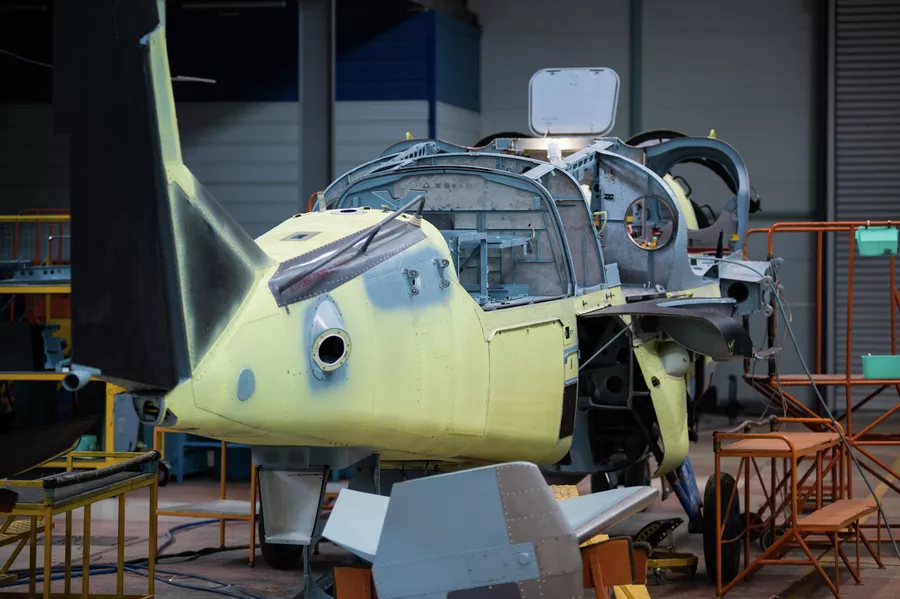
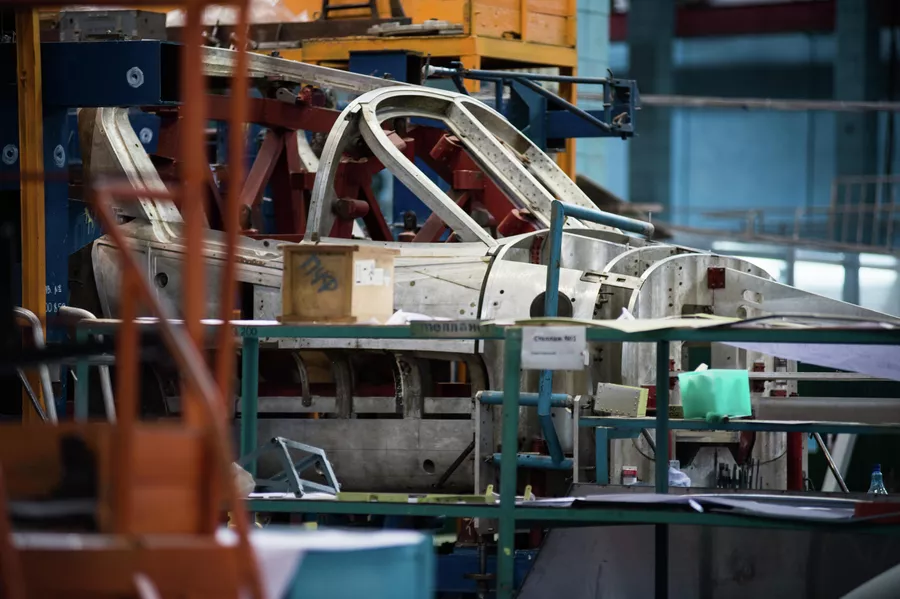
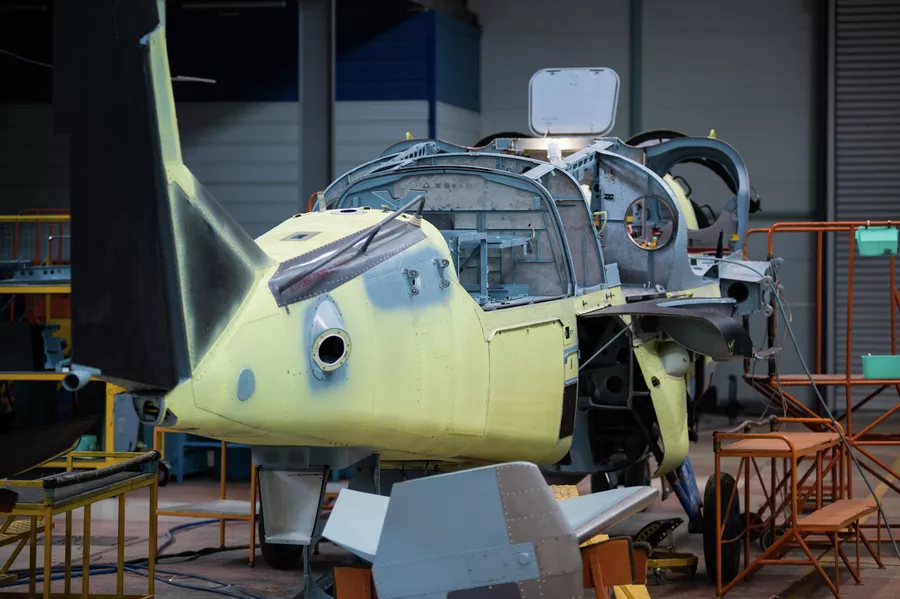
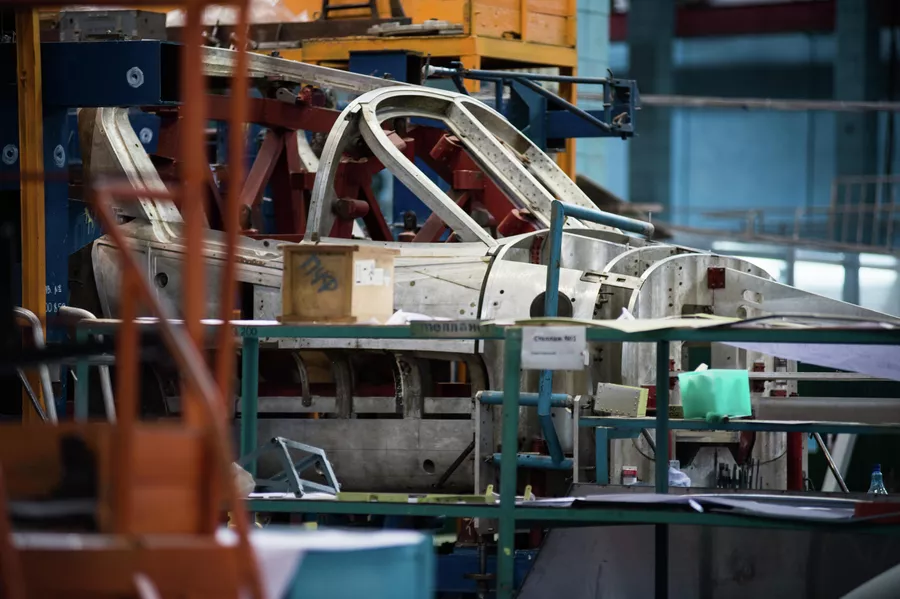
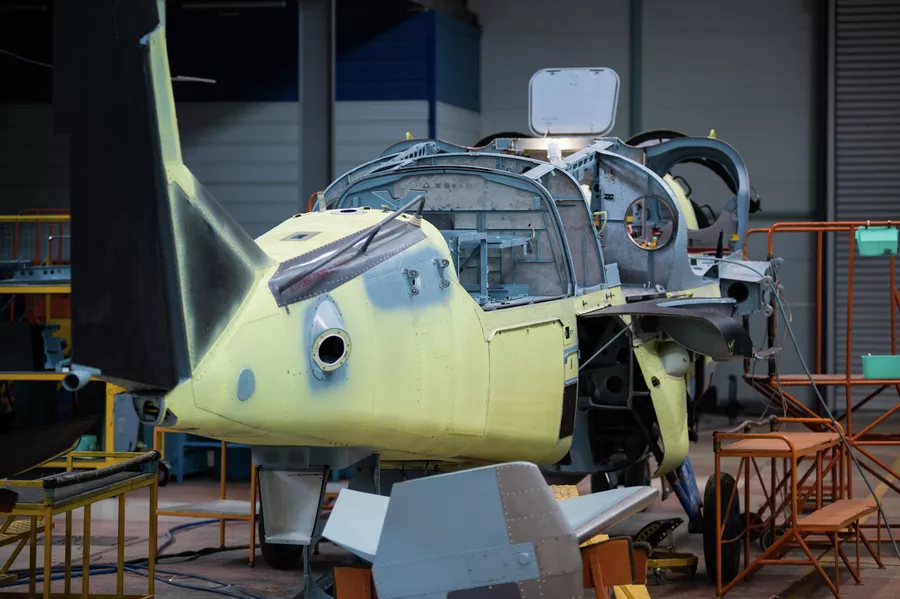
Каркас вертолета собирают в главном стапеле. Все элементы должны стыковаться идеально, без натягов, зазоров и загибов. Играют роль даже полмиллиметра.
«У нас два главных стапеля, двойная линия сборки, — начальник сборочного производства Дмитрий Коновалов ведет меня через лес металлоконструкций, попутно показывая, что снимать можно, а что нельзя. — Вначале в стапель выставляется центроплан, затем присоединяются передний и задний топливные баки, хвостовая и носовая части, все это клепается, а затем проводится нивелировка. Пожалуй, стыковка фюзеляжа — самый ответственный этап, она проводится под особым наблюдением бюро техконтроля и заказчика. Если тут напортачить, придется браковать весь вертолет».
Скелет боевой машины — титановые элементы крепления, аллюминиевые нервюры и шпангоуты подаются в цех агрегатной сборки с механических производств. Клепают их вручную, с помощью пневмоинструмента.
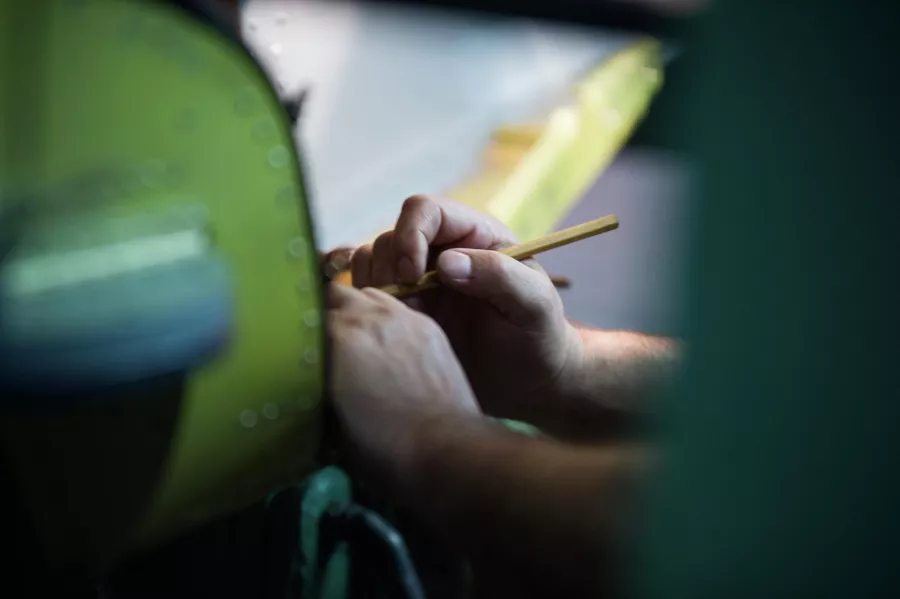
По словам рабочих, эксперименты с клепательным станком успехом не увенчались — он работает только с прямыми швами, а у «Аллигатора» фюзеляж сложной формы, со множеством выемок и изгибов.
Собраться и взлететь
После схода со стапеля начинается кропотливая установка всевозможных капотов, крыльев, технологических лючков. Для проверки жесткости на фюзеляже закрепляют массовые макеты редуктора и двигателей. Под нагрузкой проверяют плавность закрытия и открытия дверей, люков.
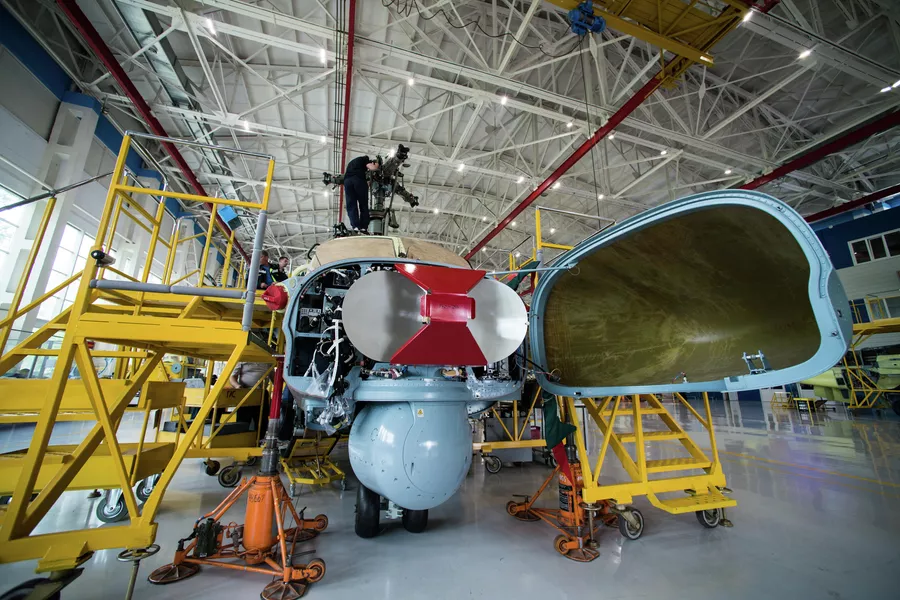
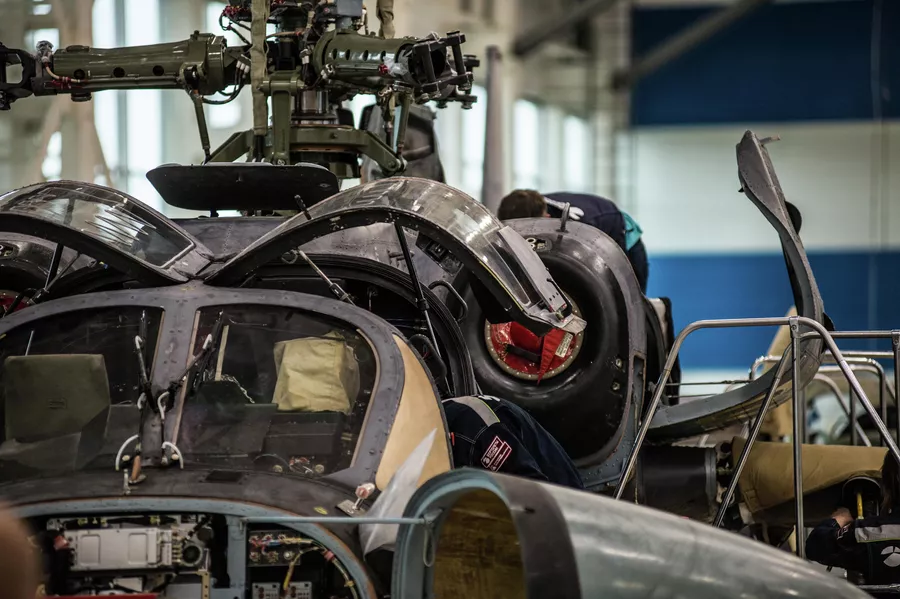
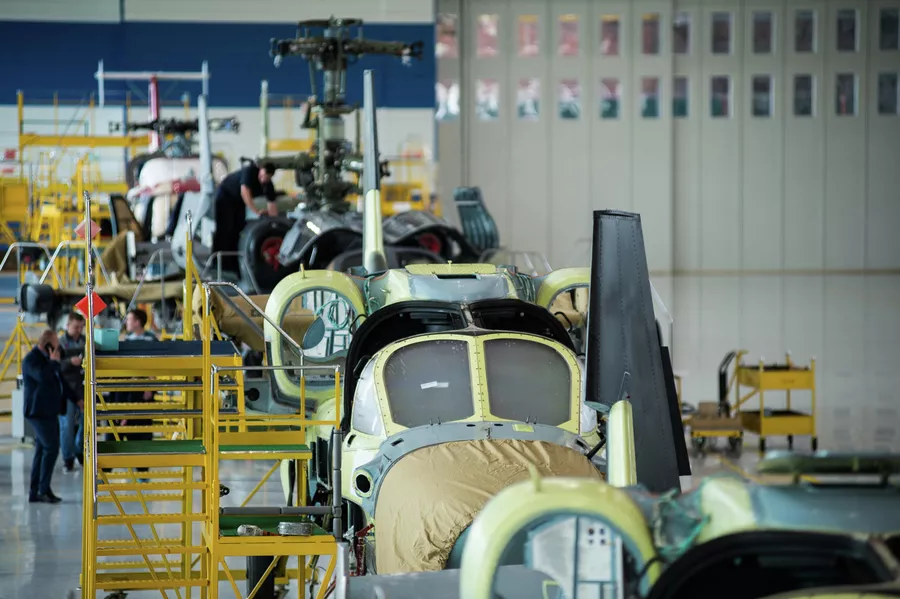
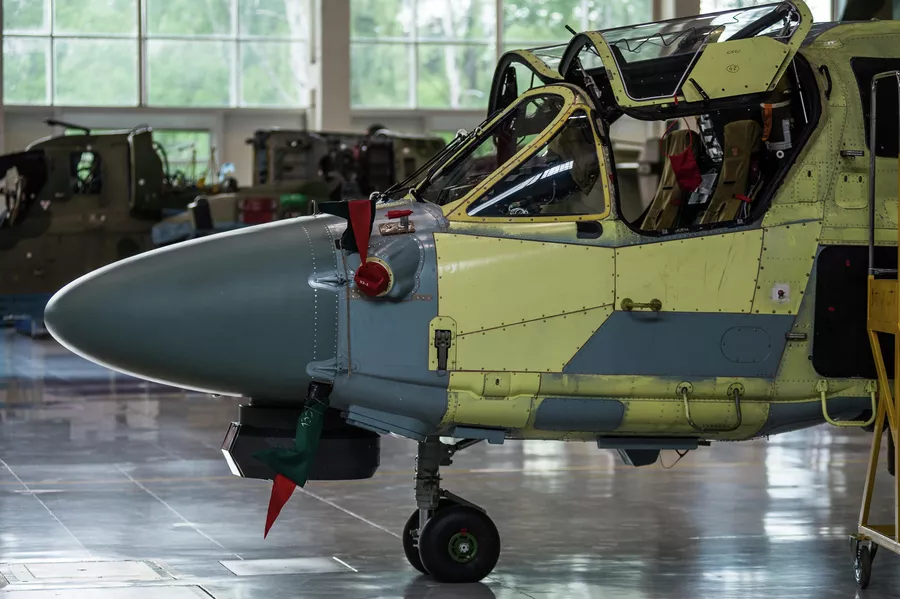
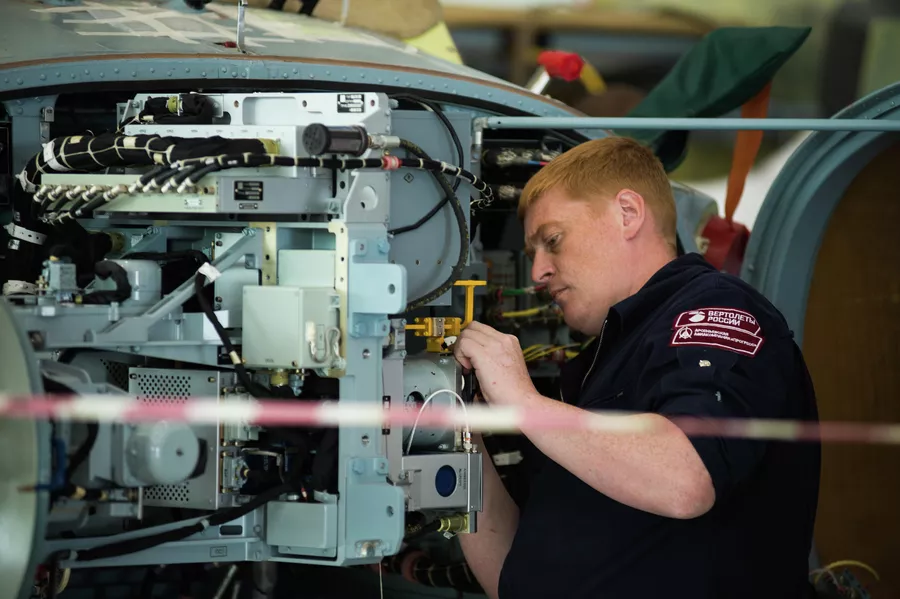
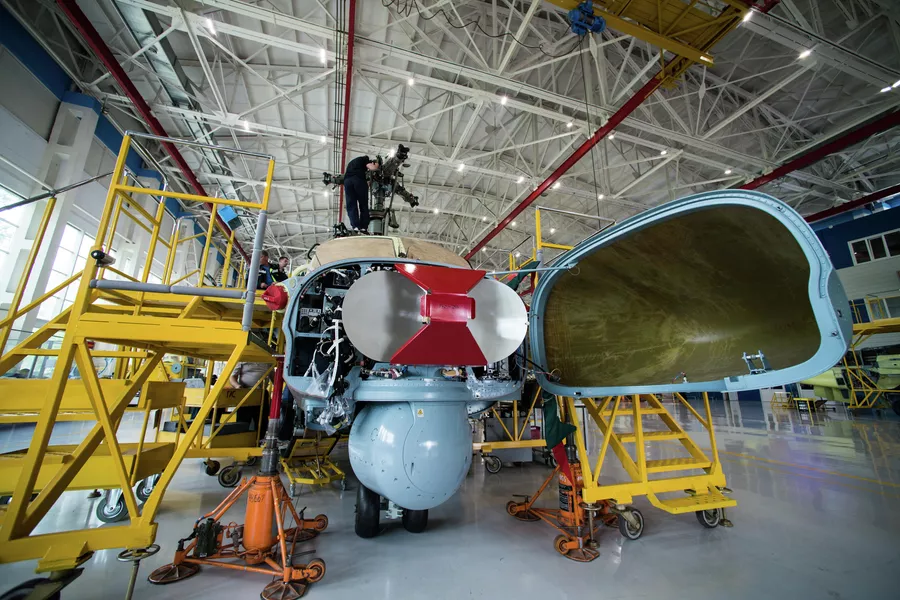
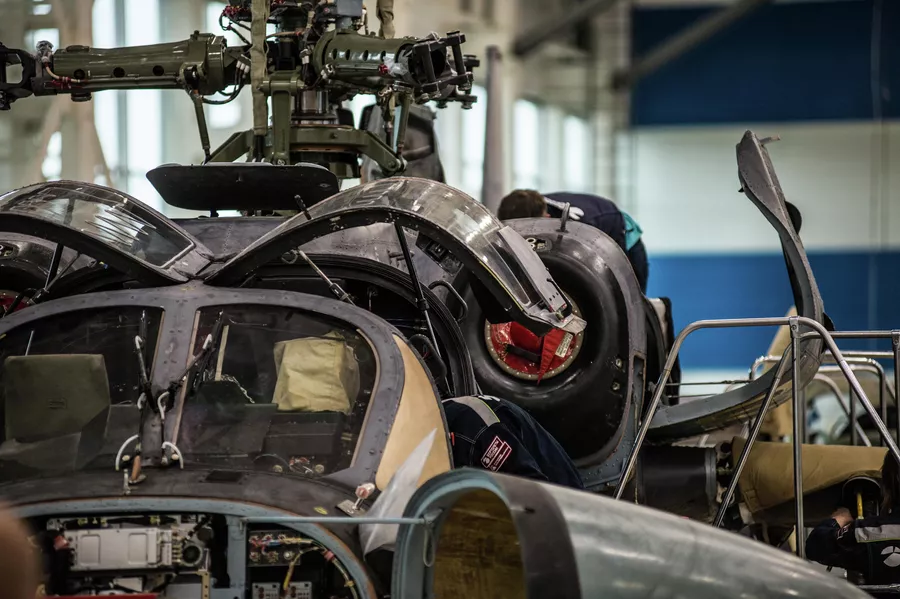
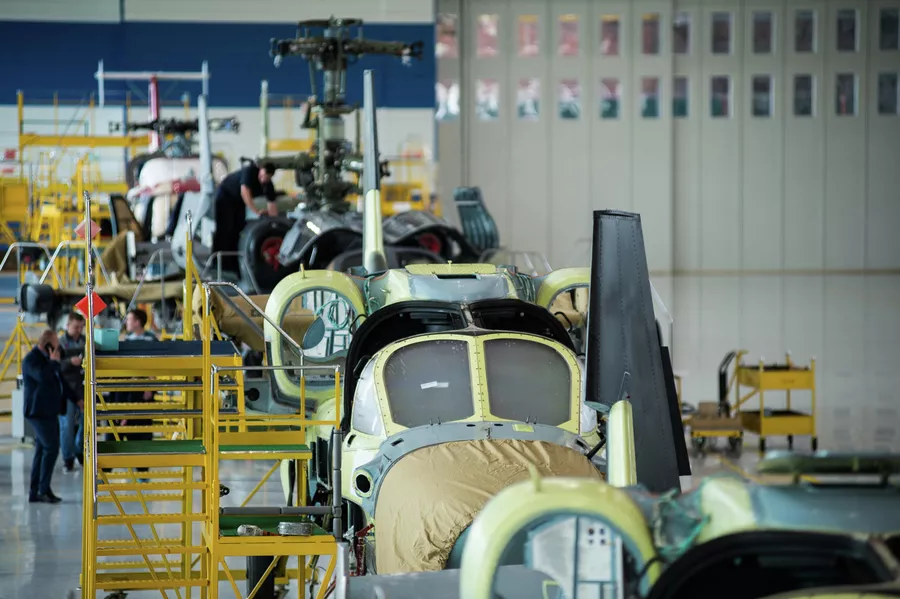
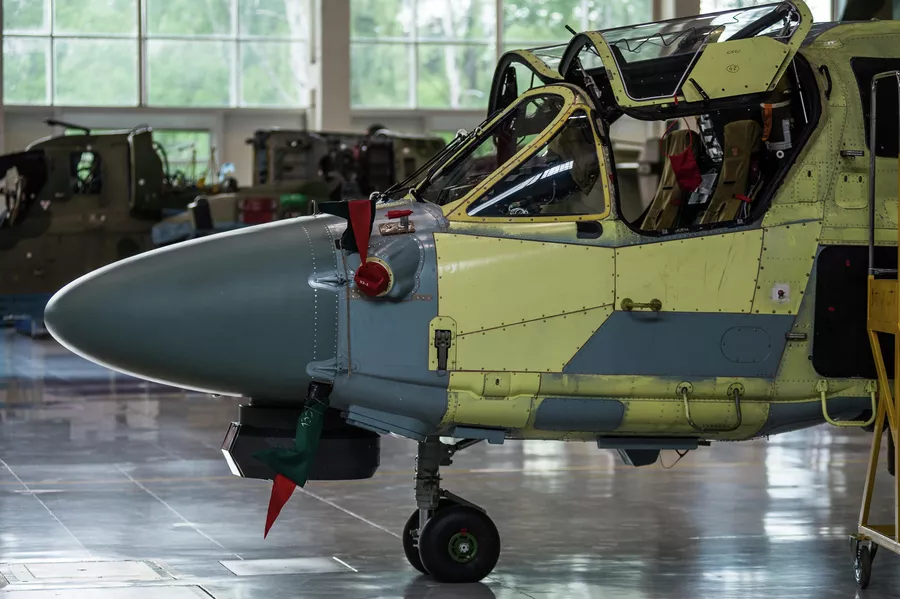
«Если все свободно закрывается-открывается и нет перекосов, закатываем фюзеляж в дождевальную камеру для проверки на герметичность, — продолжает Коновалов. — Там специальная установка со всех сторон поливает его водой под напором. Процедура занимает 20 минут. В корпусе есть водонепроницаемые зоны, под лючками — резиновые прокладки, в стыках — герметик. Внутри все должно быть сухо».
После дождевания вертолет тщательно вытирают и дотошно осматривают от носа до хвоста. В бюро технического контроля много женщин и девушек. Они и проверяют качество клепки, сборки, заполняют пачки отчетных документов и заключений.
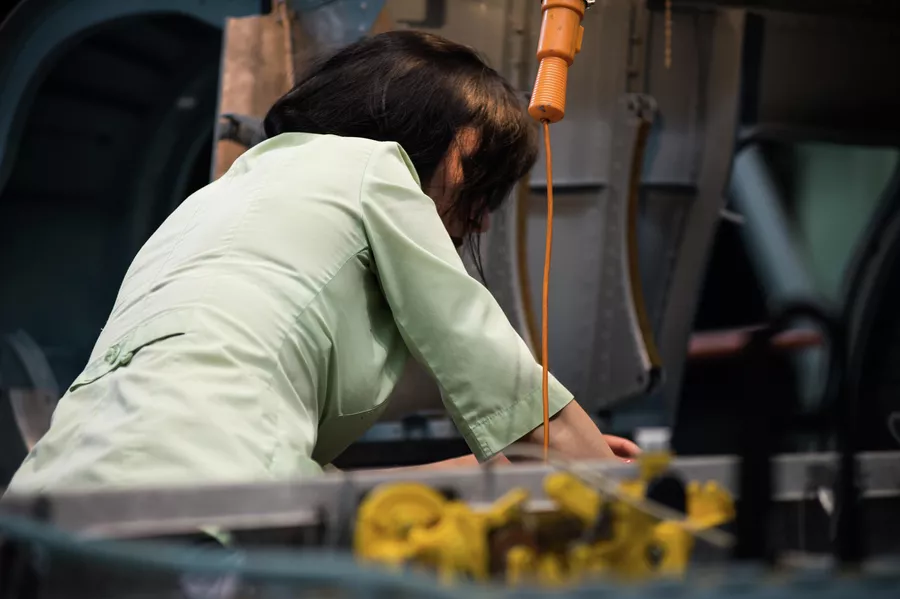
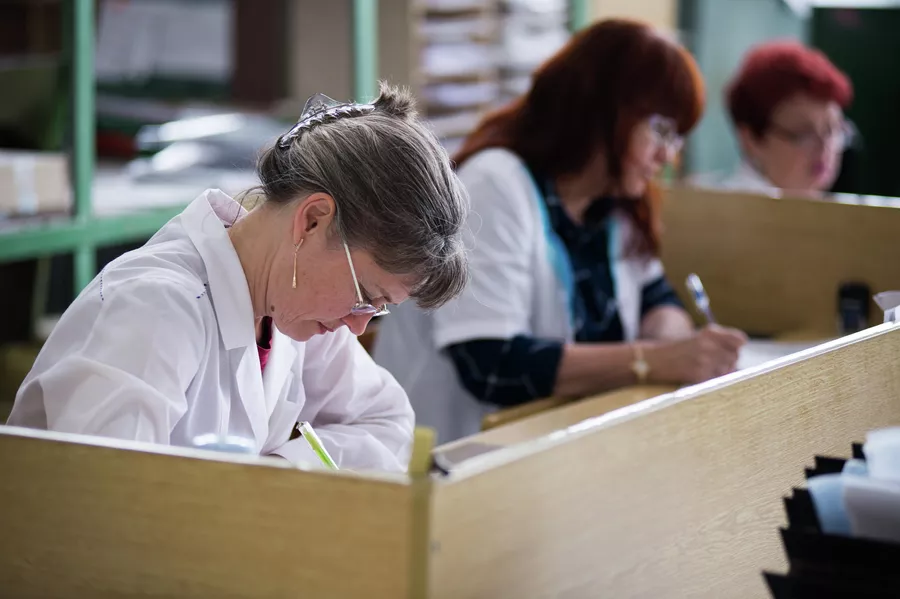
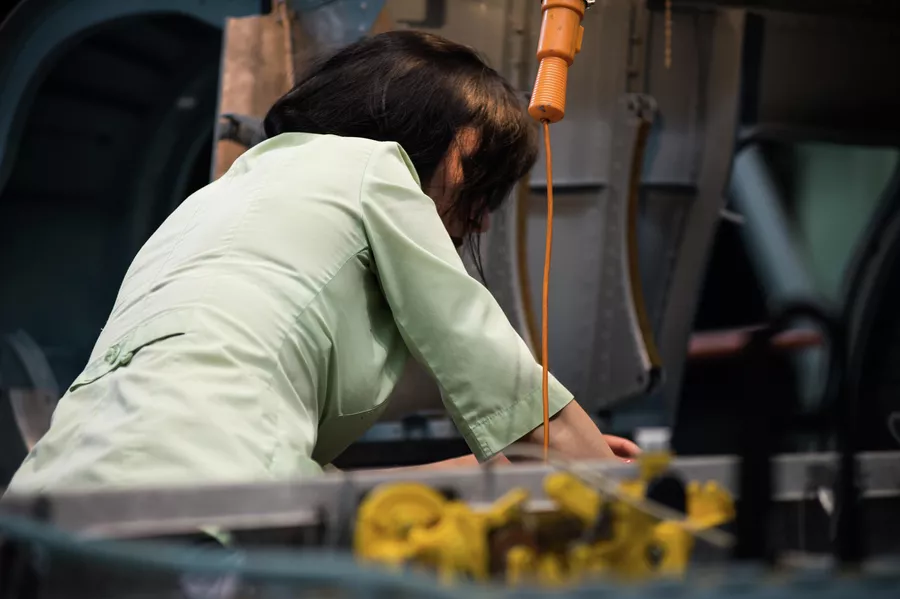
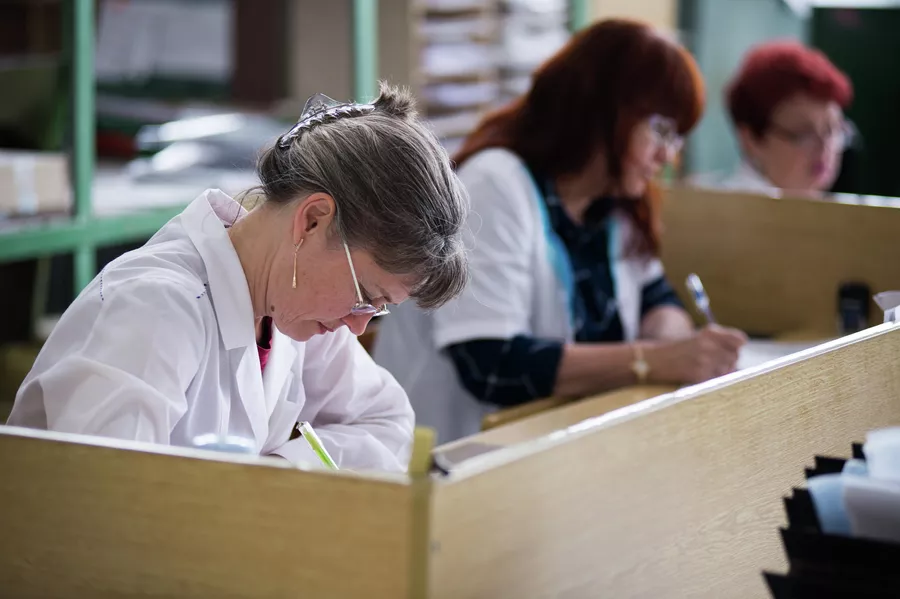
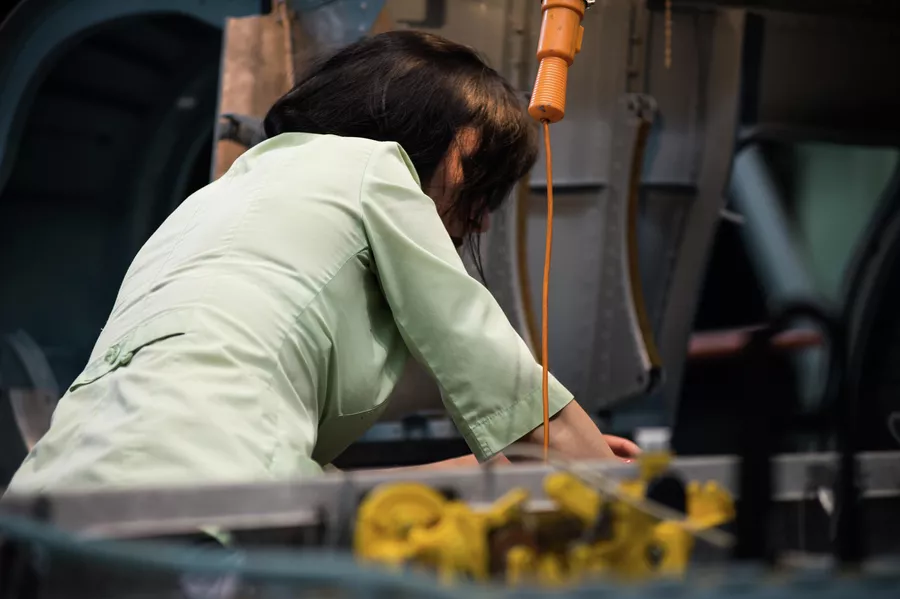
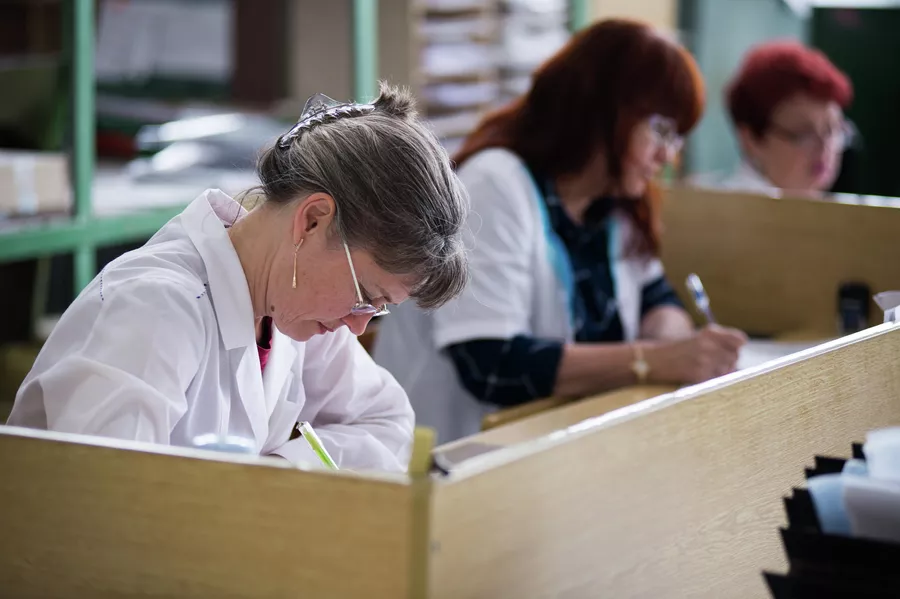
Из цеха агрегатной сборки мы с Дмитрием переходим в «чистую комнату» — цех окончательной сборки. Именно здесь форма обретает содержание и фюзеляж становится боевым вертолетом — «Аллигатором». В цехе царит почти идеальная чистота — параметры среды строго контролируются специальными датчиками, развешанными по стенам.
«Первым делом в фюзеляже монтируют трубки топливной, противопожарной и гидравлической систем, — объясняет Коновалов. — Затем трассами выкладывают электропроводку. Каждый жгут тщательно проверяем на порезы и забоины, их быть не должно — категорически. Когда все «вены» и «жилы» — электроэлементы — протянуты, ставим электроагрегаты».
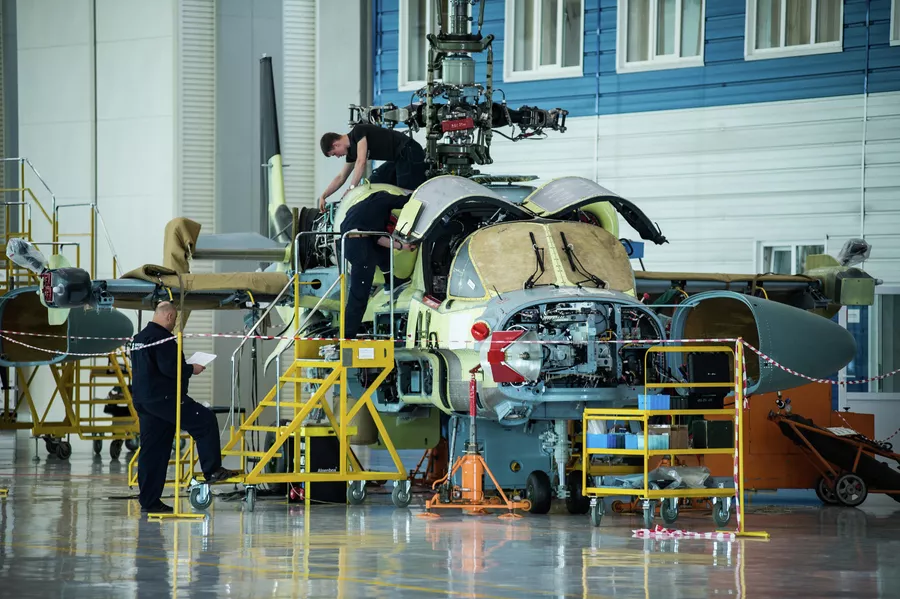
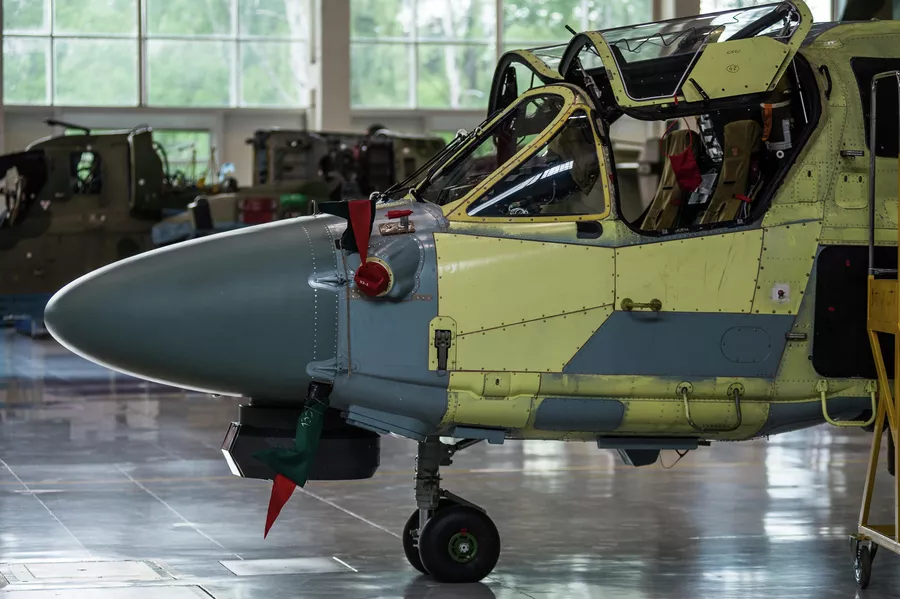
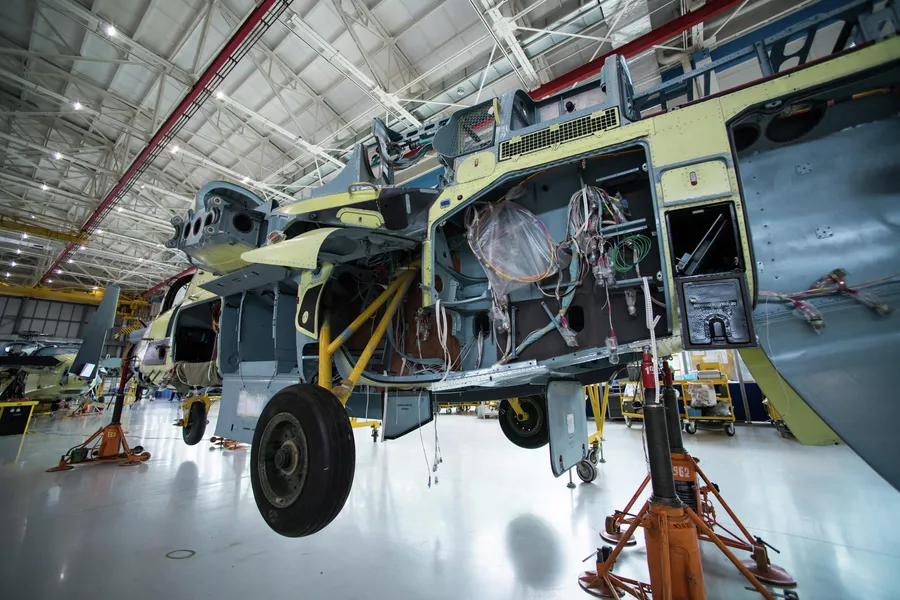
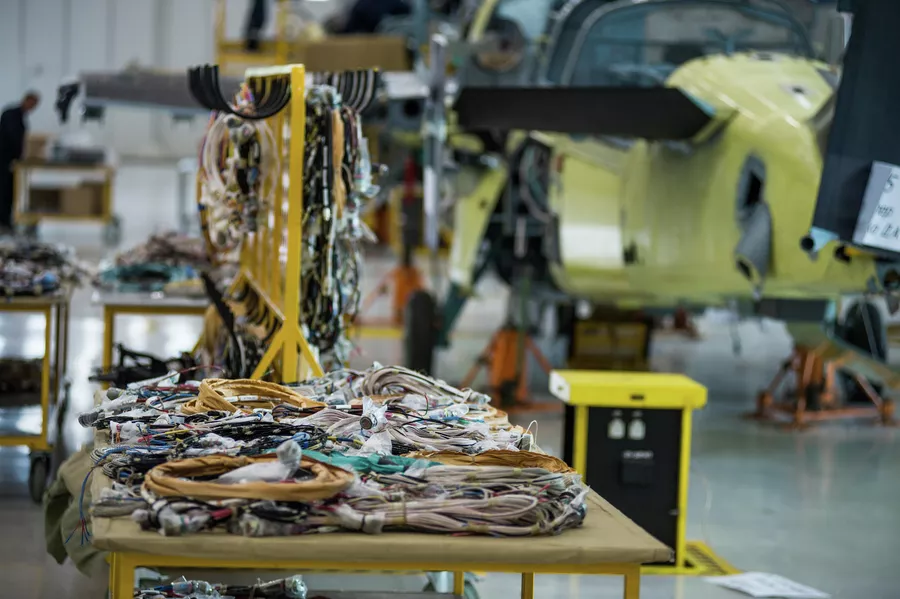
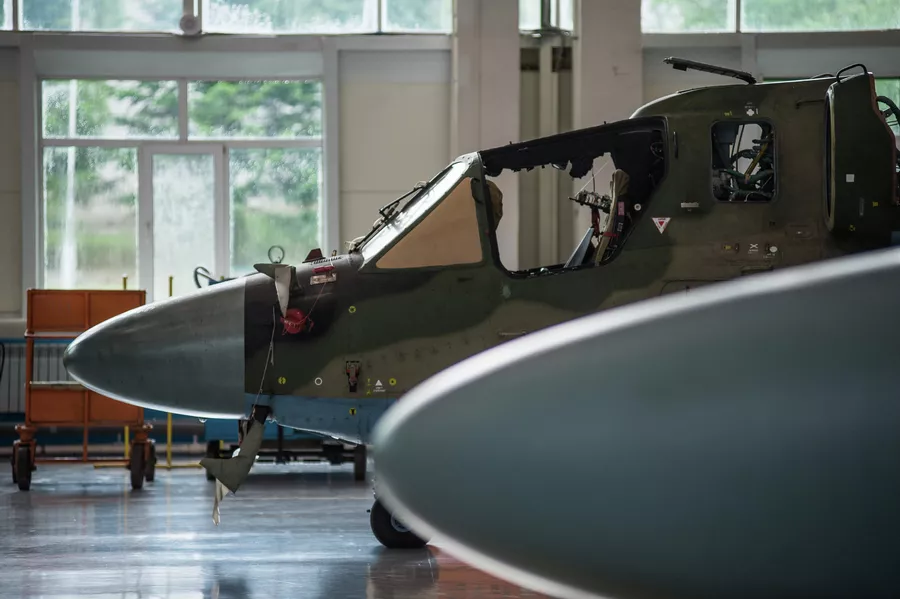
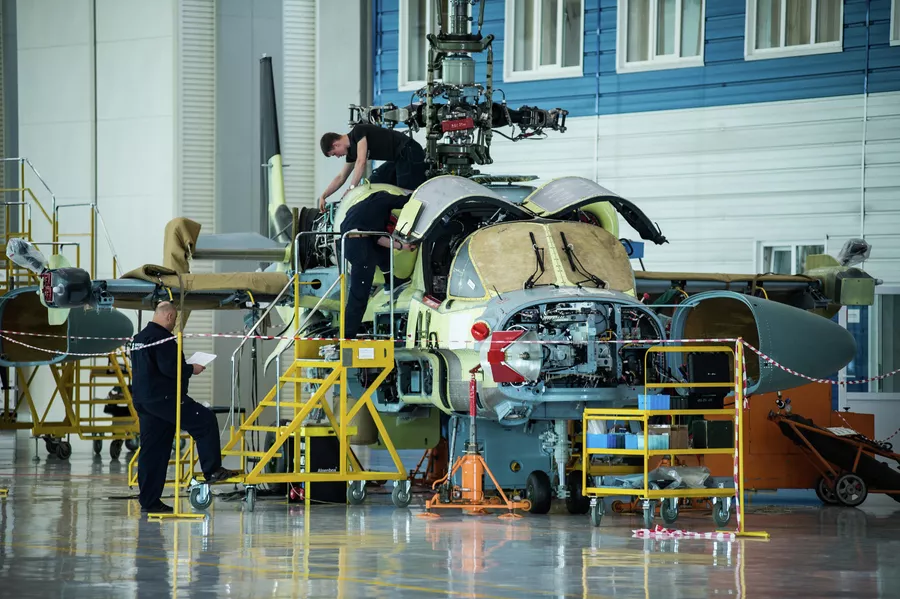
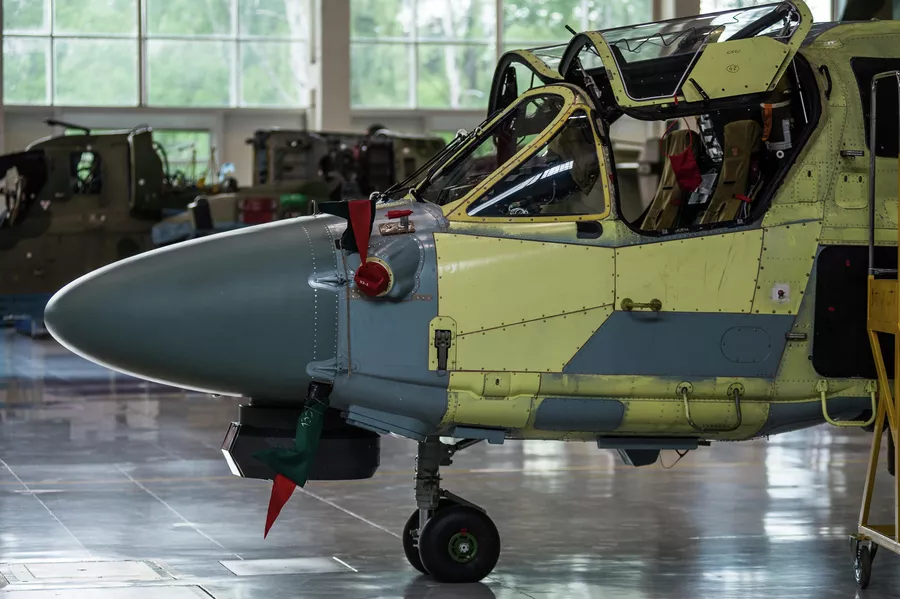
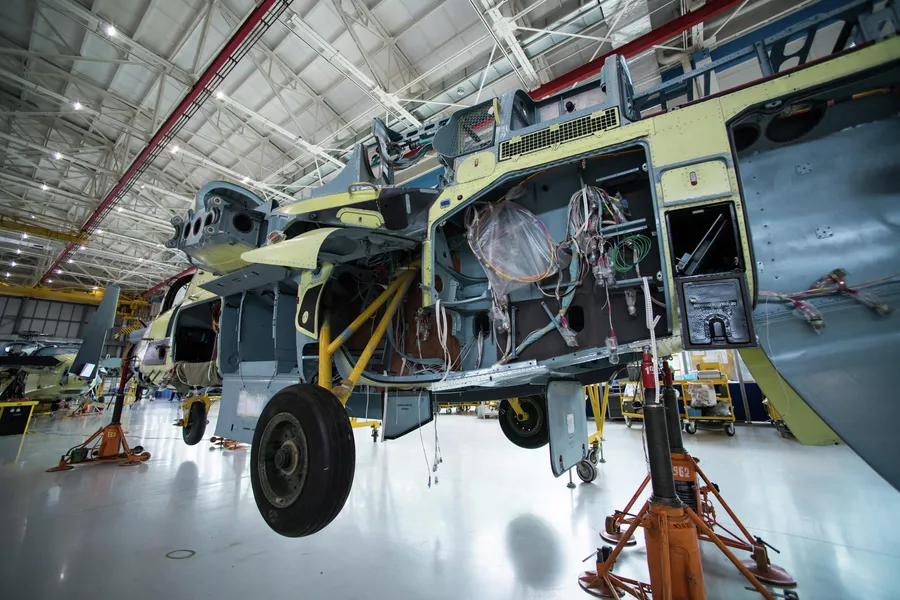
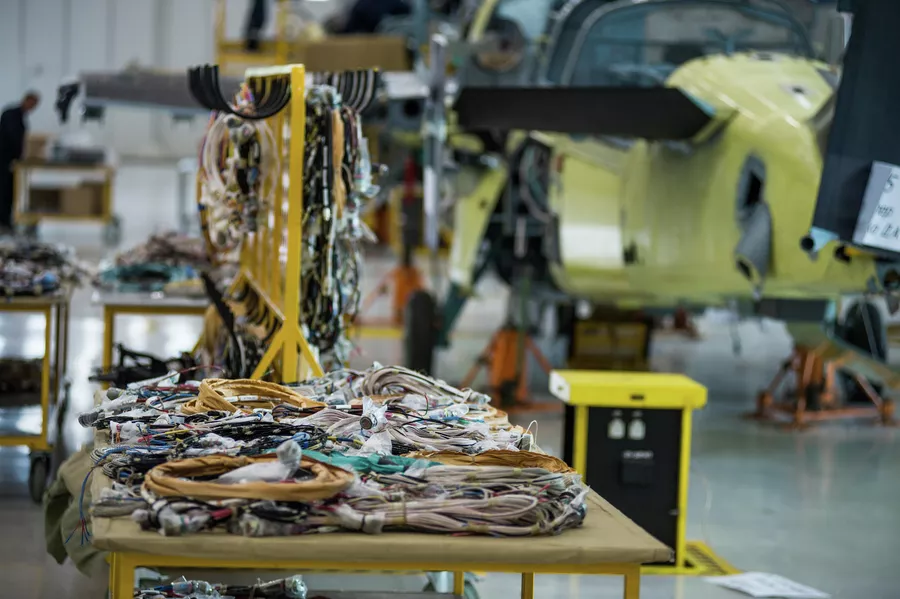
В среднем цикл окончательной сборки одного вертолета занимает 44 дня. Финальный штрих — монтаж редуктора и двигателей силовой установки. Их у «Аллигатора» два — турбовальные ВК-2500 петербургского производства. От ТВ3-117ВМА, применяемых на большинстве «милевских» и «камовских» машин, они отличаются повышенной мощностью: поднимают Ка-52 на высоту до пяти тысяч метров.
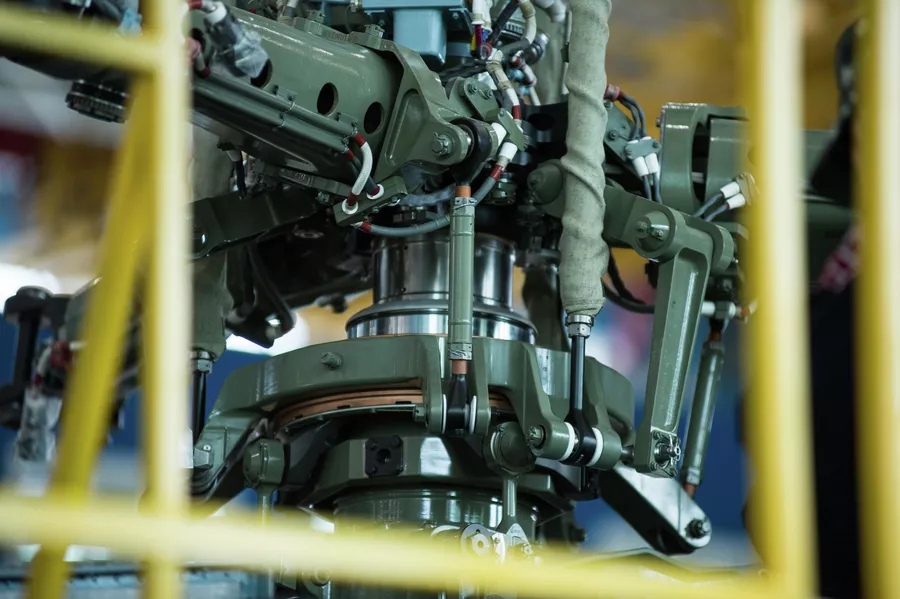
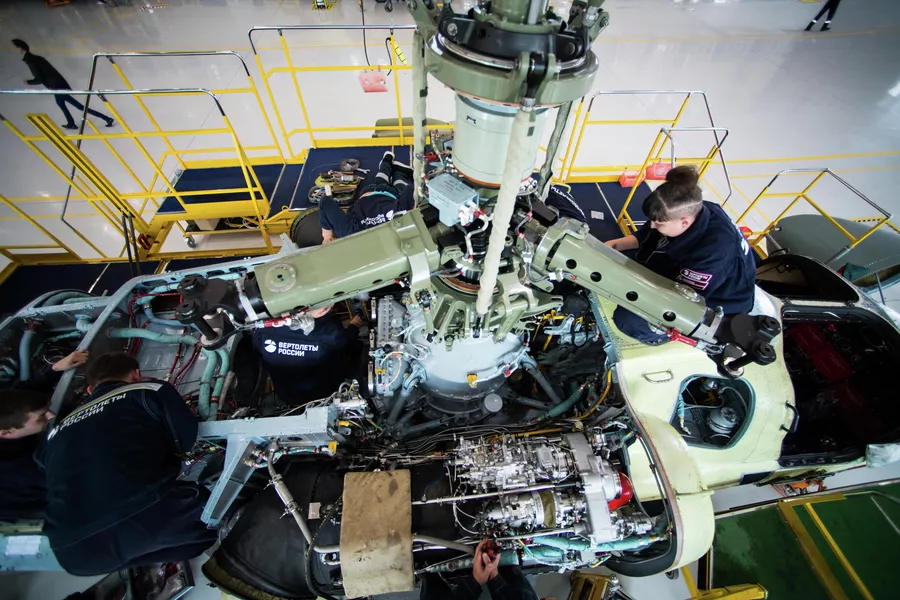
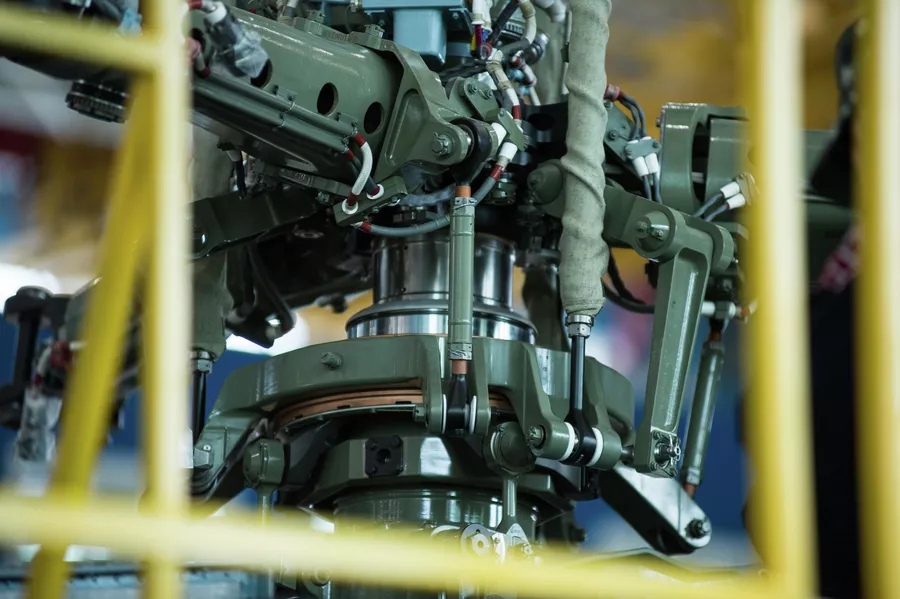
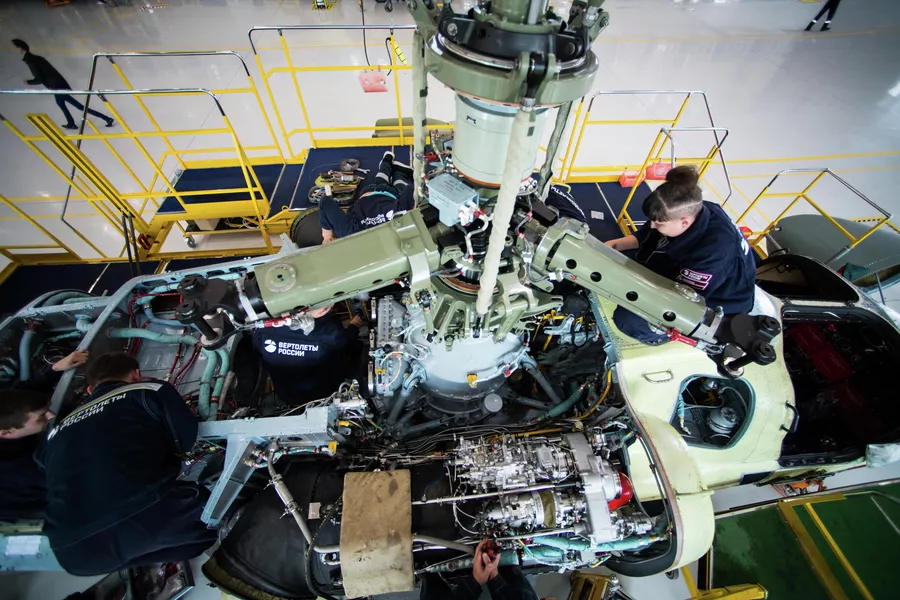
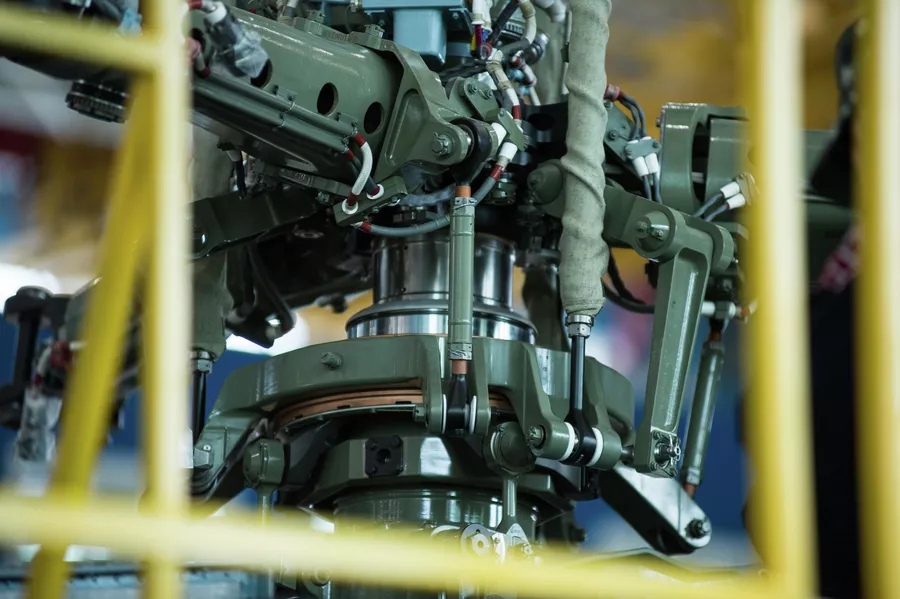
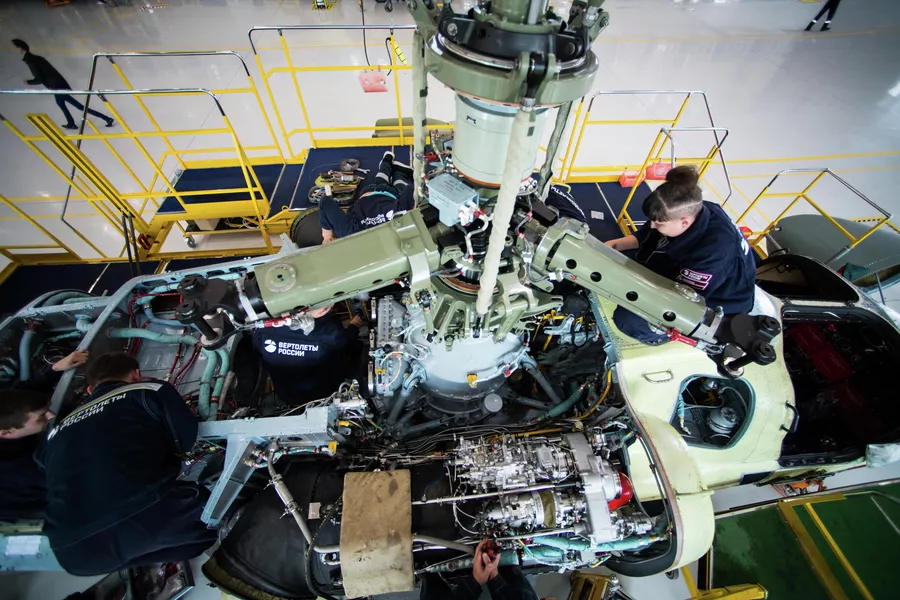
Когда двигатели на месте, все трубки скручены, электроразъемы подстыкованы, вертолет в «тысячный раз» осматривают представители бюро техконтроля и военной приемки.
Хищная стрекоза войны
Если замечаний нет, машину «хлопают по боку» и передают в контрольно-испытательный цех, где ставят бортовое вооружение и приводят в боевую готовность для передачи на летно-испытательную станцию.
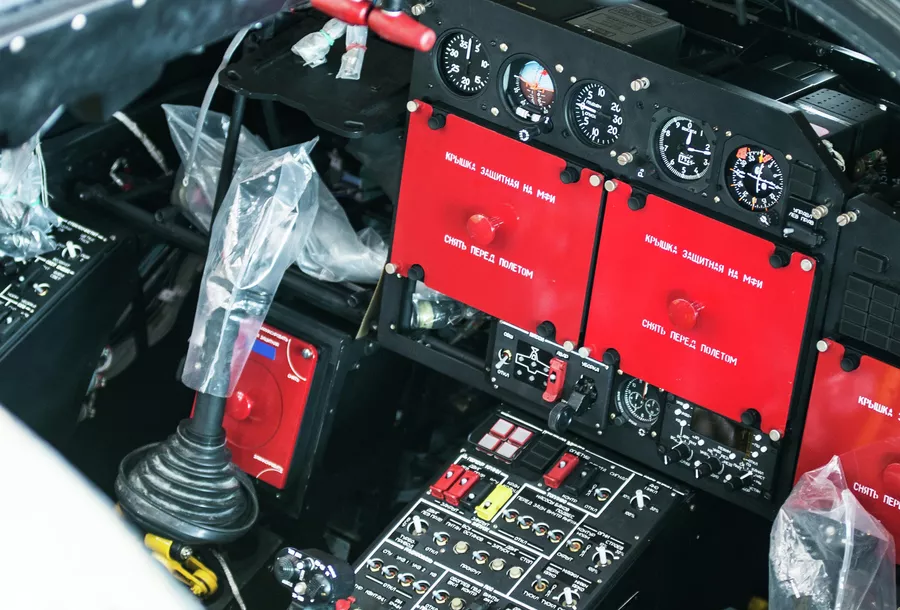
«Вначале каждый вертолет тестируют наши «прогрессовские» инженеры и летчики, — отмечает Дмитрий. — Производят настройку двигателей, редуктора, испытывают несущие винты на устойчивость к флаттеру (разрушительным вибрациям. — Прим. ред.). Военным передаем уже облетанные изделия. Вообще, по отзывам самих летчиков, «пятьдесят второй» ведет себя в полете очень послушно, жалоб нет».
Сотрудники «Прогресса» очень гордятся тем, что их завод — единственный в стране, который делает такие уникальные боевые машины.
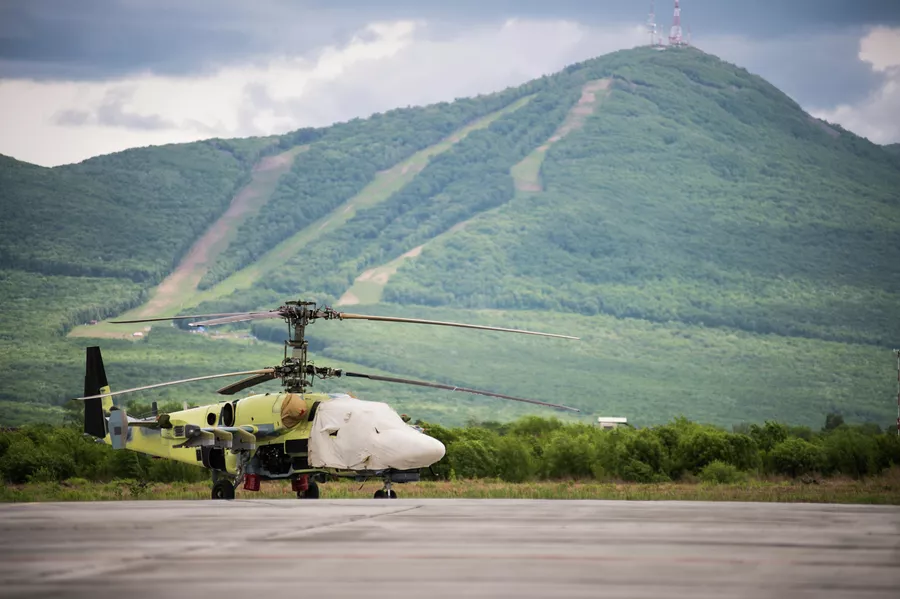
Фирменных «фишек» у Ка-52 хватает: соосная схема несущих винтов, система спасения летчиков с отстрелом лопастей, необычная для ударного вертолета компоновка кабины экипажа «бок о бок», мощная броня, компактность и малозаметность.
По боевой нагрузке, скорости и потолку «Аллигаторы» на голову превосходят главных конкурентов: американские АН–64D Apache Longbow и франко-германские Eurocopter Tiger.
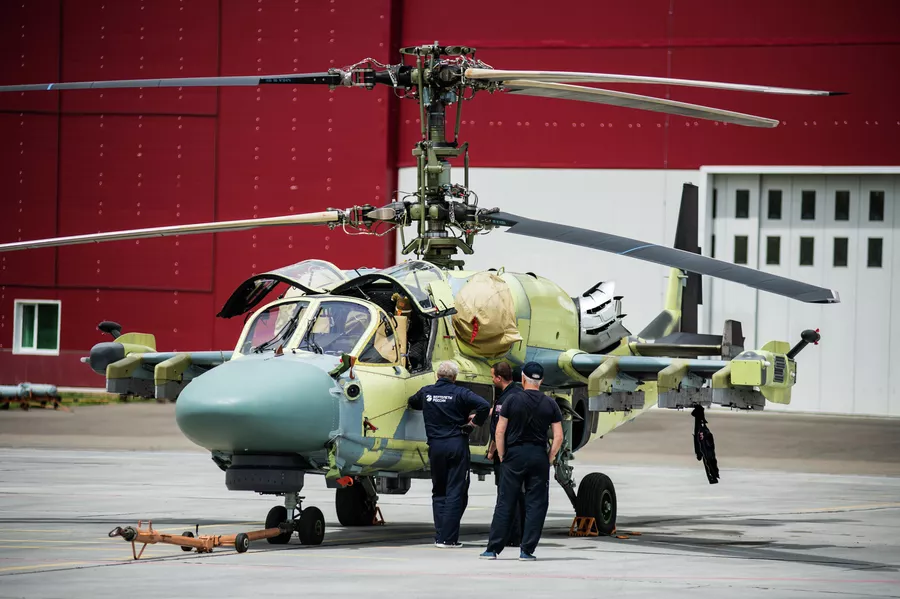
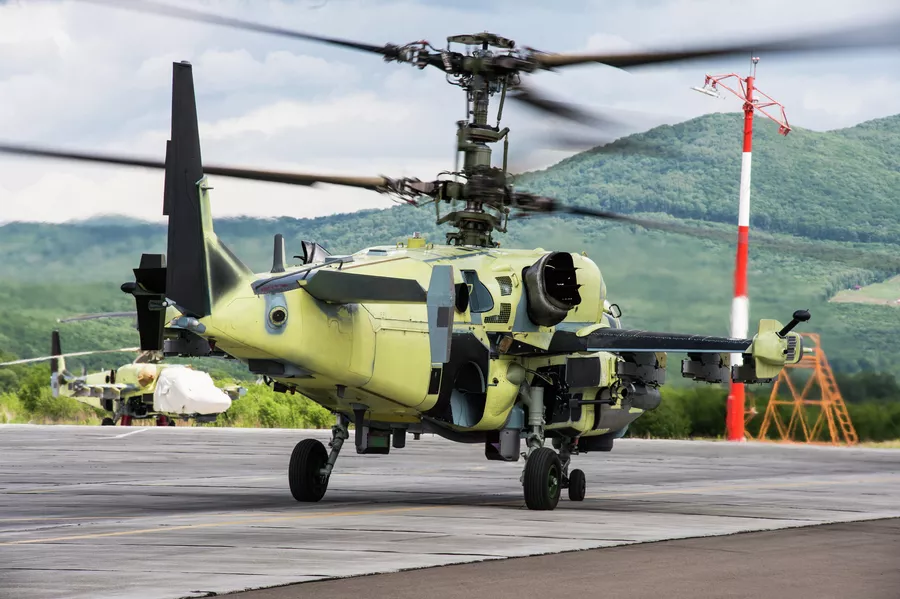
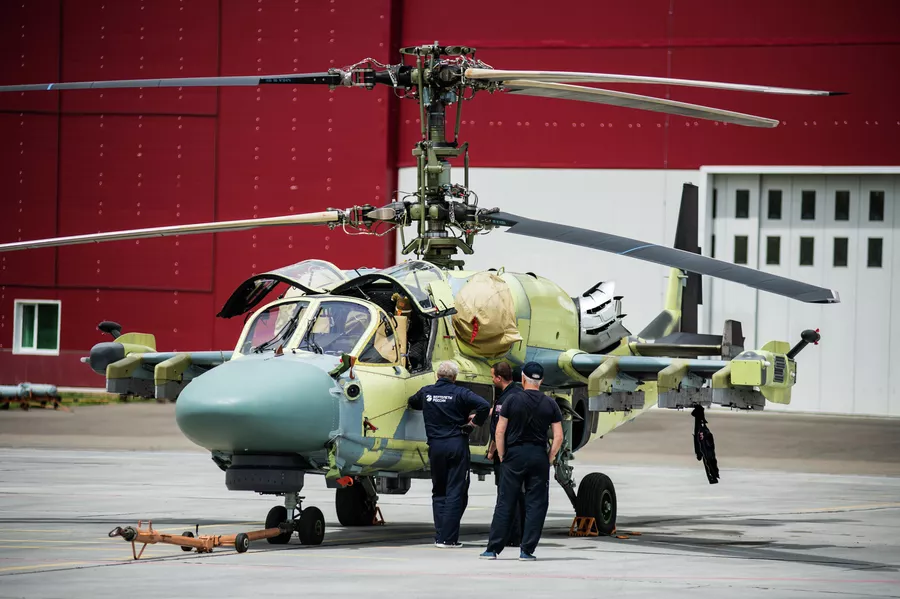
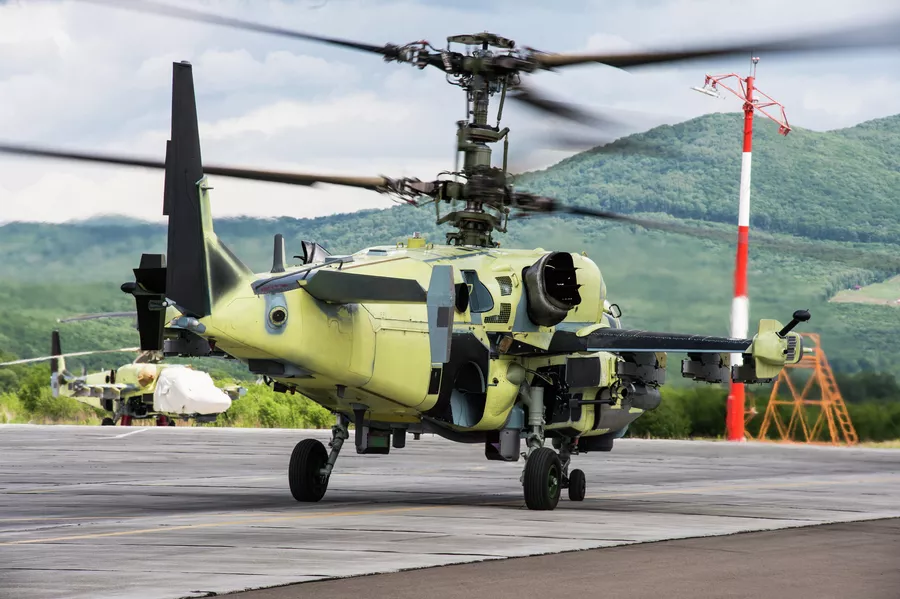
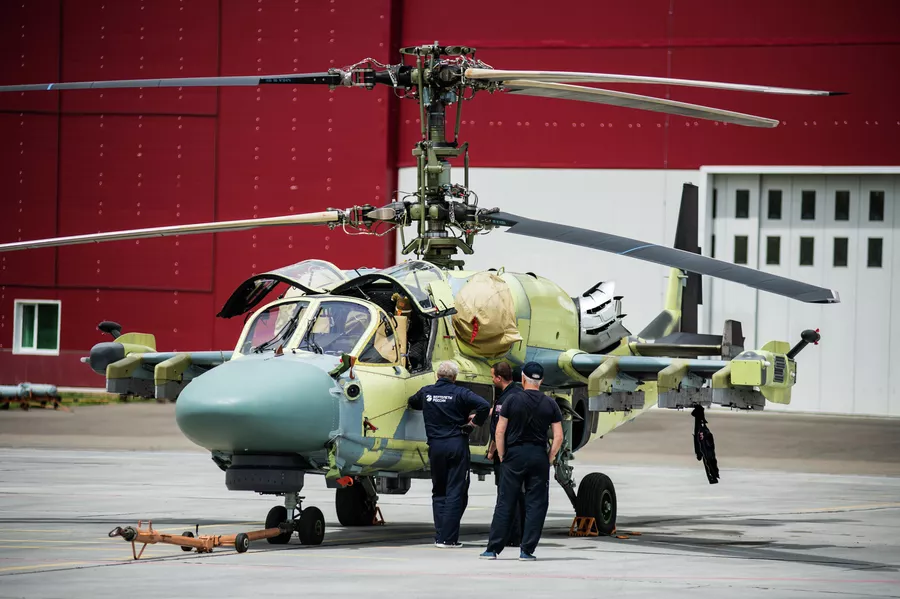
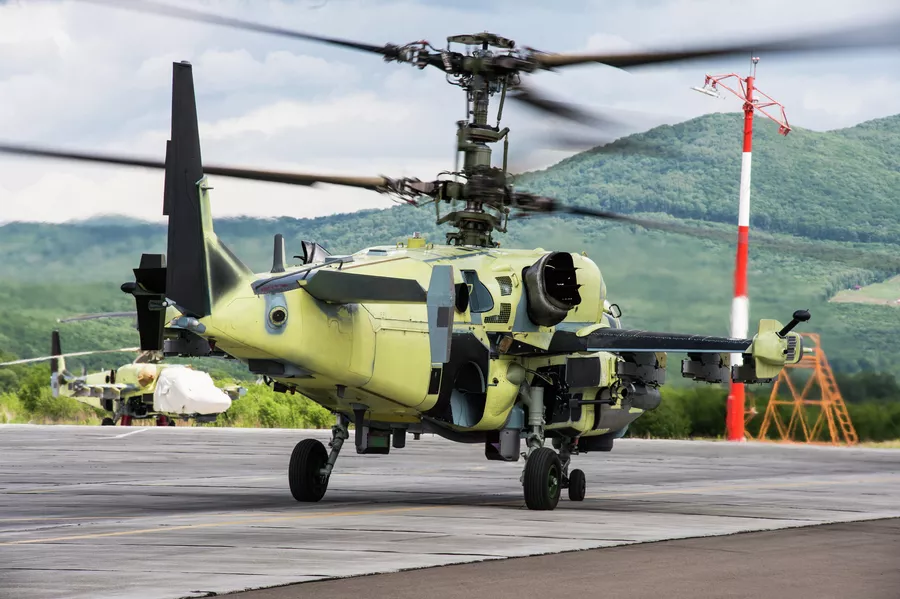
Российский вертолет вооружен 30-миллиметровой пушкой 2А42-1, может оснащаться ракетным комплексом «Стрелец», нести управляемые ракеты типа «Атака» и «Вихрь-1», а также контейнеры неуправляемых ракет типа С-8. Этого арсенала за глаза хватает для отработки бронетехники и живой силы вероятного противника.
Хищный силуэт и глухой стук винтов приближающегося «Аллигатора» ни с чем не спутаешь. Глядя на эту машину с земли, подсознательно понимаешь: очень не хотелось бы оказаться с ней по разные стороны линии фронта. Даже ненадолго.